Manufacturing method of surface adhered light-emitting element lamp group
A surface-adhering, light-emitting element technology, applied in the field of process design of semiconductor light-emitting element lamp sets, to achieve the effect of saving man-hours, increasing efficiency and precise positioning
- Summary
- Abstract
- Description
- Claims
- Application Information
AI Technical Summary
Problems solved by technology
Method used
Image
Examples
Embodiment Construction
[0052] The specific embodiments adopted by the present invention will be further described through the following embodiments and accompanying drawings.
[0053] refer to figure 1 As shown, it is a flow chart showing the steps of the preferred embodiment of the present invention, and at the same time coordinates Figure 2 to Figure 12 A description of the preferred embodiments of the present invention is as follows.
[0054] refer to figure 2 , image 3 and Figure 4 , first prepare a rod body S with a predetermined length L and a winding frame T with corresponding rotating drive shafts T1, T2 (step 101). Then the rod S is combined with the rotating drive shafts T1 and T2 of the winding frame T, and the rotating driving shafts T1 and T2 are driven to rotate by a winding device E (step 102 ).
[0055] refer to Figure 5 At least two wires 1, 2 with outer covering insulation layers 11, 21 are arranged at a predetermined winding distance D, when the rod body S is driven to ...
PUM
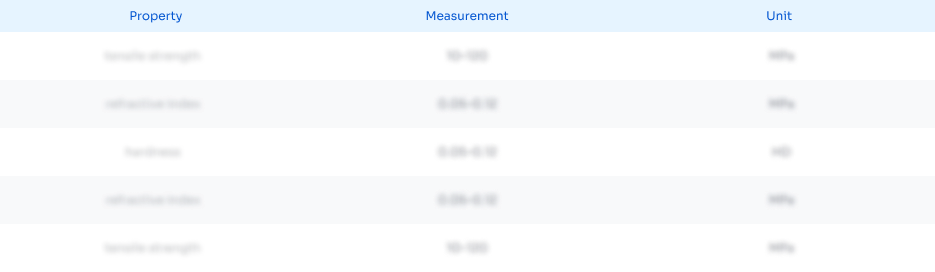
Abstract
Description
Claims
Application Information

- R&D
- Intellectual Property
- Life Sciences
- Materials
- Tech Scout
- Unparalleled Data Quality
- Higher Quality Content
- 60% Fewer Hallucinations
Browse by: Latest US Patents, China's latest patents, Technical Efficacy Thesaurus, Application Domain, Technology Topic, Popular Technical Reports.
© 2025 PatSnap. All rights reserved.Legal|Privacy policy|Modern Slavery Act Transparency Statement|Sitemap|About US| Contact US: help@patsnap.com