Preparation method of vacuum ultraviolet excited green silicate fluorescent powder
A green fluorescent powder and vacuum ultraviolet technology, which is applied in the direction of luminescent materials, chemical instruments and methods, etc., can solve the problems of affecting the image quality, long afterglow time, shortening the afterglow time of phosphor powder, etc., to achieve improved luminous performance, simple process operation, The effect of shortening the afterglow time
- Summary
- Abstract
- Description
- Claims
- Application Information
AI Technical Summary
Problems solved by technology
Method used
Image
Examples
Embodiment 1
[0027] According to the green phosphor Zn 1.92-x-2y Mg x Y y Li y SiO 4 :0.0gMn 2+ The stoichiometric ratio of silicic acid, zinc oxide, manganese acetate, magnesium oxide, yttrium oxide and lithium carbonate were mixed to form the starting raw material, and the ratio of adding 1ml of absolute ethanol to 10 grams of starting raw material was used to obtain absolute ethanol , adding absolute ethanol to the starting material for ball milling, mixing evenly to obtain a raw material powder; putting the raw material powder into a tube furnace, keeping it warm for 5 hours at a temperature of 1200 ° C and feeding nitrogen, and then, using The cooling rate of 1°C / min lowers the temperature in the tube furnace to 800°C. At this time, stop feeding nitrogen, and pass a mixed gas composed of 90% nitrogen and 10% hydrogen into the tube by volume percentage. Type furnace, keep warm for 5 hours, and cool with the furnace to obtain calcined powder; grind the calcined powder, then wash wi...
Embodiment 2
[0029] According to the green phosphor Zn 1.92-x-2y Mg x Y y Li y SiO 4:0.08Mn 2+ The stoichiometric ratio of silicon dioxide, zinc oxide, manganese acetate, magnesium oxide, yttrium oxide and lithium carbonate were mixed to form the starting raw material, and 3ml of absolute ethanol was added to 10 grams of starting raw material, and anhydrous Ethanol, adding absolute ethanol to the starting raw materials, grinding, and mixing uniformly to obtain raw material powders; putting the raw material powders into a tube furnace, keeping the temperature at 1350° C. and feeding nitrogen for 3 hours, and then , at a cooling rate of 6°C / min, lower the temperature in the tube furnace to 1000°C, at this time, stop feeding nitrogen, and feed a mixed gas consisting of 95% nitrogen and 5% hydrogen by volume The tube furnace is kept warm for 1 hour and cooled with the furnace to obtain calcined powder; the calcined powder is ground, then washed with deionized water, dried, and passed thro...
Embodiment 3
[0031] According to the green phosphor Zn 1.92-x-2y Mg x Y y Li y SiO 4 :0.08Mn 2+ The stoichiometric ratio of silicic acid, zinc oxide, manganese acetate, magnesia, yttrium oxide and lithium carbonate were mixed to form the starting material, and 2ml of dehydrated alcohol was added to 10 grams of the starting material, and dehydrated alcohol was taken , adding absolute ethanol to the starting raw material, ball milling, and mixing uniformly to obtain a raw material powder; put the raw material powder into a tube furnace, and keep it warm for 4 hours at a temperature of 1275 ° C and nitrogen gas, and then, With a cooling rate of 3.5°C / min, the temperature in the tube furnace is reduced to 900°C. At this time, the feeding of nitrogen is stopped, and a mixed gas consisting of 92.5% nitrogen and 7.5% hydrogen is passed into the furnace by volume. Tube furnace, keep warm for 3 hours, and cool with the furnace to obtain calcined powder; grind the calcined powder, then wash wit...
PUM
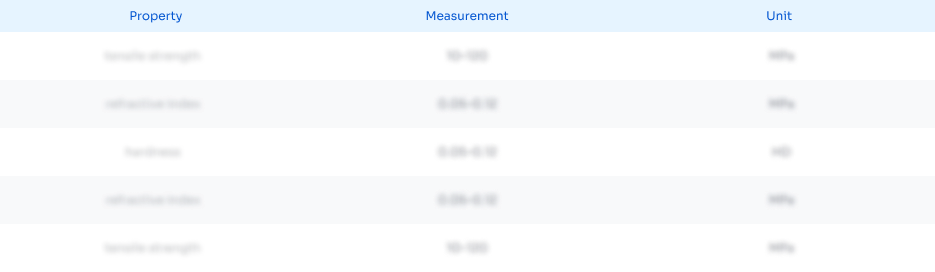
Abstract
Description
Claims
Application Information

- R&D
- Intellectual Property
- Life Sciences
- Materials
- Tech Scout
- Unparalleled Data Quality
- Higher Quality Content
- 60% Fewer Hallucinations
Browse by: Latest US Patents, China's latest patents, Technical Efficacy Thesaurus, Application Domain, Technology Topic, Popular Technical Reports.
© 2025 PatSnap. All rights reserved.Legal|Privacy policy|Modern Slavery Act Transparency Statement|Sitemap|About US| Contact US: help@patsnap.com