Ceramic-based friction material and method for preparing same
A friction material and ceramic-based technology, which is applied in the field of ceramic-based friction materials and its preparation, can solve the problems of easily scratched friction couples, unstable friction performance, poor braking flatness and flexibility, etc., and achieve low braking noise and high friction coefficient. Moderate, smooth braking effect
- Summary
- Abstract
- Description
- Claims
- Application Information
AI Technical Summary
Problems solved by technology
Method used
Examples
Embodiment 1
[0052] 1. Preheat and disperse the potassium titanate whiskers until the potassium titanate whiskers have a diameter of 1.5um and a length of 100um.
[0053] Mix the raw materials according to the following proportions, and the particle size of the ingredients is mostly above 200 mesh:
[0054] 6kg of thermoplastic phenolic resin or its modified products; 8kg of potassium titanate whiskers; 5kg of attapulgite; 4kg of expanded vermiculite; 4kg of nitrile rubber powder; 5kg of chromite powder; 12kg of ceramic fiber; 4kg of coke powder; ; Artificial graphite 6kg; flake graphite 9kg; organic friction powder 8kg; sericite 3kg; alumina 1kg; copper fiber 3kg; colorant 4kg; organic fiber 0.5kg.
[0055] The organic friction powder is cashew nut oil friction powder; the colorant is iron yellow, iron red or iron black; and the organic fiber is aramid fiber.
[0056] 2. Cold press forming: the pressure is 180kg / cm 2 .
[0057] 3. Hot pressing molding: temperature is 155°C, pressure is...
Embodiment 2
[0062] 1. Preheat and disperse the potassium titanate whiskers until the potassium titanate whiskers have a diameter of 0.2um and a length of 10um.
[0063] Mix the raw materials according to the following proportions, and the particle size of the ingredients is mostly above 200 mesh:
[0064] 8kg of modified thermoplastic phenolic resin; 7kg of potassium titanate whiskers; 6kg of attapulgite; 3kg of expanded vermiculite; 5kg of nitrile rubber powder; 4kg of chromite powder; 13kg of ceramic fiber; Graphite 5kg; flake graphite 10kg; organic friction powder 7kg; sericite 4kg; alumina 0.5kg; copper fiber 4kg; colorant 3kg; organic fiber 1kg.
[0065] The organic friction powder is cashew nut oil friction powder; the colorant is iron yellow, iron red or iron black; and the organic fiber is aramid fiber.
[0066] 2. Cold press forming: the pressure is 200kg / cm 2 .
[0067] 3. Hot pressing: temperature is 160℃, pressure is 250kg / cm 2 , the pressing speed is 1 mm / min.
[0068] 4...
PUM
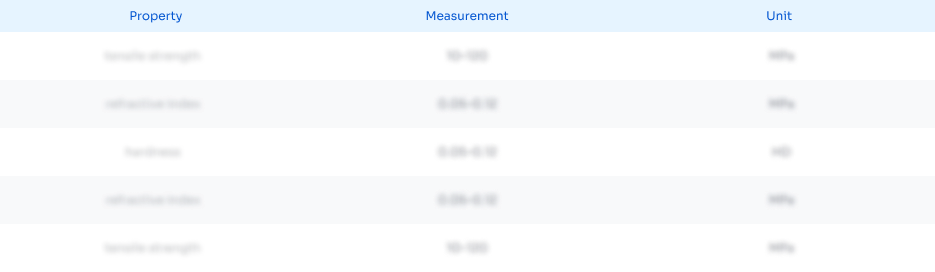
Abstract
Description
Claims
Application Information

- R&D
- Intellectual Property
- Life Sciences
- Materials
- Tech Scout
- Unparalleled Data Quality
- Higher Quality Content
- 60% Fewer Hallucinations
Browse by: Latest US Patents, China's latest patents, Technical Efficacy Thesaurus, Application Domain, Technology Topic, Popular Technical Reports.
© 2025 PatSnap. All rights reserved.Legal|Privacy policy|Modern Slavery Act Transparency Statement|Sitemap|About US| Contact US: help@patsnap.com