Method for simultaneously smelting zinc dipping slag and zinc kiln slag by using blast furnace
A zinc leaching slag and blast furnace technology, which is applied in the field of extracting valuable metal elements in zinc kiln slag and zinc leaching slag, can solve the problems of sulfur dioxide deterioration treatment environment, unsatisfactory zinc volatilization index, sulfur dioxide pollution environment and other problems, and achieve simple and practical equipment , Good separation effect, environment-friendly effect
- Summary
- Abstract
- Description
- Claims
- Application Information
AI Technical Summary
Problems solved by technology
Method used
Image
Examples
Embodiment 1
[0026] Get zinc dipping slag (main content is: Zn is 5-20%; Pb is 3.2-3.5%; Cd is 0.2-0.3%; Cu is 1.0%; Fe is 1.8-5%; As is 0.8-1.0%; Sb 0.3-0.3%; Ag is 0.022-0.03%; In is 0.05-0.06%; S is 6-7%) 400kg, the initial particle size -200 mesh accounts for 75%, is mixed with 10% water, and then in the disc system The agglomeration is carried out in the agglomeration machine to obtain the zinc leaching slag agglomerate, which is naturally dried in a ventilated place for 10 hours and then enters the batching process section. Take zinc kiln slag (the main content is: CuO is 1.12%, TFe is 31.36%, Zn is 8.15%, Ag is 119.3g / t, In is 198.4g / t) material 46%, the initial particle size of zinc kiln slag requires + 10 mesh accounts for 75%; add 15% coke with a fixed carbon content of 74%, 5% SiO 2 The content is more than 98% of silica and 34% of zinc leaching slag. The four materials are mixed by a circular mixer and then melted in a blast furnace. The process conditions controlled by the b...
Embodiment 2
[0028] Get zinc dipping slag (main content is: Zn is 5-20%; Pb is 3.2-3.5%; Cd is 0.2-0.3%; Cu is 1.0%; Fe is 1.8-5%; As is 0.8-1.0%; Sb 0.3-0.3%; Ag is 0.022-0.03%; In is 0.05-0.06%; S is 6-7%) 400kg, the initial particle size -200 mesh accounts for 75%, is mixed with 15% of water, and then in the disc system The agglomeration is carried out in the agglomeration machine to obtain the zinc leaching slag agglomerate, which is naturally dried in a ventilated place for 14 hours and then enters the batching process section. Take zinc kiln slag (main content: CuO is 1.12%, TFe is 31.36%, Zn is 8.15%, Ag is 119.3g / t, In is 198.4g / t) material 53%, the initial particle size of zinc kiln slag requires + 10 mesh accounts for 85%; add 15% coke with a fixed carbon content of 74%, 4% SiO 2 The content is more than 98% of silica and 28% of zinc leaching slag. The four materials are mixed by a circular mixer and then melted in a blast furnace. The process conditions controlled by the blast...
Embodiment 3
[0030] Get zinc dipping slag (main content is: Zn is 5-20%; Pb is 3.2-3.5%; Cd is 0.2-0.3%; Cu is 1.0%; Fe is 1.8-5%; As is 0.8-1.0%; Sb Ag is 0.3-0.3%; Ag is 0.022-0.03%; In is 0.05-0.06%; S is 6-7%) 400kg, the initial particle size -200 mesh accounts for 75%, is mixed with 20% of water, and then in the disc system The agglomeration is carried out in the agglomeration machine to obtain the zinc leaching slag agglomerate, which is naturally dried in a ventilated place for 16 hours and then enters the batching process section. Take zinc kiln slag (main content: CuO is 1.12%, TFe is 31.36%, Zn is 8.15%, Ag is 119.3g / t, In is 198.4g / t) material 60%, the initial particle size of zinc kiln slag requires + 10 mesh accounts for 95%; add 15% coke with a fixed carbon content of 74%, 2% SiO 2 The content is more than 98% of silica and 23% of zinc leaching slag. The four materials are mixed by a circular mixer and then melted in a blast furnace. The process conditions controlled by the...
PUM
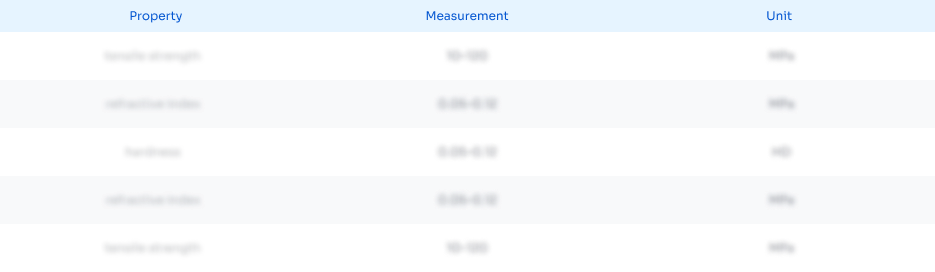
Abstract
Description
Claims
Application Information

- R&D
- Intellectual Property
- Life Sciences
- Materials
- Tech Scout
- Unparalleled Data Quality
- Higher Quality Content
- 60% Fewer Hallucinations
Browse by: Latest US Patents, China's latest patents, Technical Efficacy Thesaurus, Application Domain, Technology Topic, Popular Technical Reports.
© 2025 PatSnap. All rights reserved.Legal|Privacy policy|Modern Slavery Act Transparency Statement|Sitemap|About US| Contact US: help@patsnap.com