Process for smelting magnesium through melting reduction
A process and technology for smelting magnesium, applied in the field of production of metal magnesium, can solve the problems of high pressure, slow reaction speed, serious environmental pollution, etc., and achieve the effects of easy operation, high recovery rate and simple reaction control.
- Summary
- Abstract
- Description
- Claims
- Application Information
AI Technical Summary
Problems solved by technology
Method used
Examples
Embodiment 1
[0030] Furnace charge ratio: Calcined dolomite, alumina, silicon dioxide and ferrosilicon account for 51%, 10%, 26% and 13% of the total charge respectively;
[0031] Implementation conditions: furnace temperature 1600°C, system pressure 1000Pa;
[0032] Implementation results: The output rate of magnesium is 72%.
Embodiment 2
[0034] Furnace charge ratio: Calcined dolomite, alumina, silicon dioxide and ferrosilicon account for 49%, 29%, 9% and 13% of the total charge, respectively
[0035] Implementation conditions: furnace temperature 1600°C, system pressure 4000Pa
[0036] Implementation results: The output rate of magnesium is 78%.
Embodiment 3
[0038] Furnace charge ratio: Calcined dolomite, alumina, silicon dioxide and ferrosilicon account for 47%, 28%, 8% and 17% of the total charge, respectively
[0039] Implementation conditions: furnace temperature 1600°C, system pressure 1000Pa
[0040] Implementation results: The output rate of magnesium is 89%.
PUM
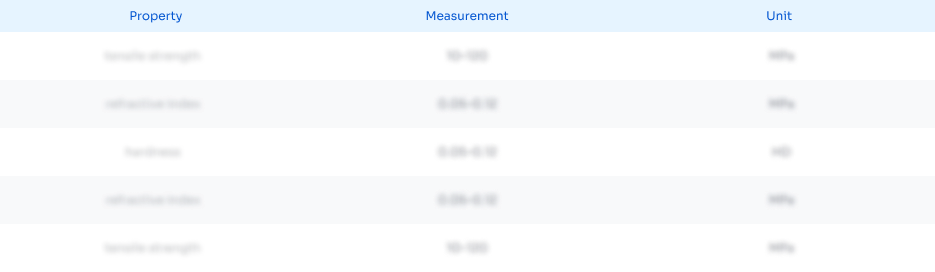
Abstract
Description
Claims
Application Information

- R&D
- Intellectual Property
- Life Sciences
- Materials
- Tech Scout
- Unparalleled Data Quality
- Higher Quality Content
- 60% Fewer Hallucinations
Browse by: Latest US Patents, China's latest patents, Technical Efficacy Thesaurus, Application Domain, Technology Topic, Popular Technical Reports.
© 2025 PatSnap. All rights reserved.Legal|Privacy policy|Modern Slavery Act Transparency Statement|Sitemap|About US| Contact US: help@patsnap.com