Ultraviolet cured flame-retardant coating and preparation method thereof
A technology of flame-retardant coatings and ultraviolet light, which is applied in the direction of fire-resistant coatings, coatings, etc., to achieve good flame-retardant effects
- Summary
- Abstract
- Description
- Claims
- Application Information
AI Technical Summary
Problems solved by technology
Method used
Image
Examples
Embodiment 1
[0048] The first step, synthesis of halogenated epoxy acrylate X-EA
[0049] According to the molar ratio of halogenated epoxy resin epoxy group to acrylic acid of 1-1.05:1, add catalyst tertiary amine or quaternary ammonium salt and phenolic polymerization inhibitor, and react at 100-110°C for 3 hours , react at 118-125°C for 2 hours under temperature control, and detect the acid value < 3mgKOH / g to obtain X-EA.
[0050] Among them, the halogenated epoxy resin can be replaced by chlorine and bromine elements, and generally the effect of bromine is better. The catalyst tertiary amine or quaternary ammonium salt is any one of triethylamine or tetraethylammonium bromide, and the dosage is 0.1-0.3% of the mass of acrylic acid. The phenolic polymerization inhibitor is hydroquinone or p-hydroxyanisole, and the dosage is 0.05-0.1% of the mass of acrylic acid.
[0051] The second step, synthesis of phosphate acrylate compound PA
[0052] Slowly add 1.1 moles of phosphorus pentoxid...
Embodiment 2
[0061] The first step is to synthesize halogenated epoxy acrylate, according to the molar ratio of halogenated epoxy resin epoxy group to acrylic acid is 1.05:1, add catalyst and polymerization inhibitor, and control the temperature at 100-110°C for 3 hours , control the temperature at 118-125 degrees for 2 hours, and detect the acid value <3mgKOH / g, you can get X-EA
[0062] The second step, synthetic phosphate ester acrylate PA: phosphorus pentoxide in molar ratio: hydroxy chloroacrylate is 1: 1.1., phosphorus pentoxide is added in the hydroxypropyl chloroacrylate, stir while adding, control The temperature is ≤95°C. After the addition, the temperature is controlled at 85-110°C. After two hours, the halogenated propylene oxide is added. At 85-95°C, the reaction can be detected for 3 hours and the acid value reaches 5-8mgKOH / g. Stop the reaction;
[0063] The third step, by weight percentage, weighs 25% of halogenated epoxy acrylate X-EA, 20% of aliphatic polyurethane acrylat...
Embodiment 3
[0065] The first step is to synthesize halogenated epoxy acrylate, according to the molar ratio of halogenated epoxy resin epoxy group to acrylic acid is 1.05:1, add catalyst and polymerization inhibitor, and control the temperature at 100-110°C for 3 hours , control the temperature at 118-125 degrees for 2 hours, and detect the acid value <3mgKOH / g, you can get X-EA
[0066] The second step is to synthesize phosphate ester acrylate PA: the molar ratio of phosphorus pentoxide: hydroxy chloroacrylate is 1: 1.2. Add phosphorus pentoxide to hydroxy chloroacrylate, stir while adding, and control the temperature ≤95°C, after adding, control the temperature at 85-110°C, add halogenated propylene oxide two hours later, at 85-95°C, react for 3 hours and stop the reaction when the acid value reaches 5-8mgKOH / g;
[0067] The third step, by weight percentage, weighs 30% of halogenated epoxy acrylate X-EA, 10% of aliphatic polyurethane acrylate PUA, 7% of phosphate acrylate PA, and 7% of ...
PUM
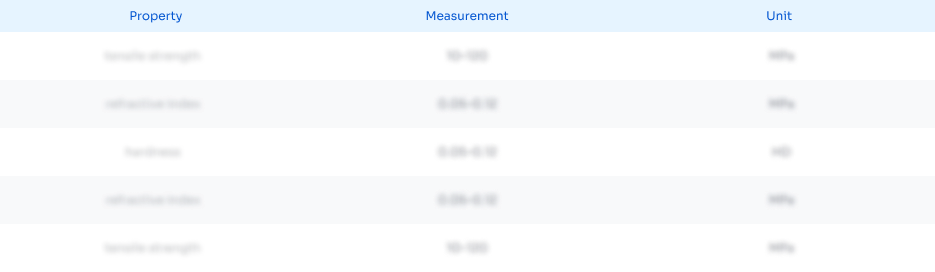
Abstract
Description
Claims
Application Information

- R&D Engineer
- R&D Manager
- IP Professional
- Industry Leading Data Capabilities
- Powerful AI technology
- Patent DNA Extraction
Browse by: Latest US Patents, China's latest patents, Technical Efficacy Thesaurus, Application Domain, Technology Topic, Popular Technical Reports.
© 2024 PatSnap. All rights reserved.Legal|Privacy policy|Modern Slavery Act Transparency Statement|Sitemap|About US| Contact US: help@patsnap.com