High thermal conducting composite material and preparation method thereof
A composite material and high thermal conductivity technology, applied in the direction of heat exchange materials, chemical instruments and methods, etc., can solve the problems of undisclosed thermal conductive filler particle size, undisclosed formula and preparation method, material performance impact, etc., to achieve low cost , good thermal conductivity and processing performance, the effect of simple process
- Summary
- Abstract
- Description
- Claims
- Application Information
AI Technical Summary
Problems solved by technology
Method used
Examples
Embodiment 1
[0031] The composition of a high thermal conductivity composite material is as follows: 100 parts of PPS, 60 parts of 200 micron alumina large particle size thermal conductive filler, 25 parts of 2 micron silicon carbide small particle size thermal conductive filler, 25 parts of glass fiber, aluminate 0.5 parts of coupling agent, 0.5 parts of molybdenum disulfide lubricant.
[0032] Its preparation method is as follows:
[0033] 1) Add a coupling agent to the 200 micron alumina weighed according to the mass ratio for surface treatment, the treatment temperature is 30-80°C, and the treatment time is 5-10 minutes;
[0034] 2) Add a coupling agent to the 2-micron silicon carbide weighed according to the mass ratio for surface treatment, the treatment temperature is 30-80°C, and the treatment time is 4-8 minutes;
[0035] 3) The polyphenylene sulfide material weighed according to the mass ratio is put into a high-speed mixer together with the treated 200 micron alumina and molybd...
Embodiment 2
[0039] The composition of a high thermal conductivity composite material is as follows: 100 parts of PP, 80 parts of 300 micron magnesium oxide, 30 parts of 5 micron aluminum nitride, 20 parts of carbon fiber, 0.5 part of aluminate coupling agent, molybdenum disulfide lubricant 0.5 parts of the agent. Its preparation method is identical with embodiment one.
example 3
[0041] The composition of a high thermal conductivity composite material is: 100 parts of PP, 60 parts of 200 micron alumina large particle size thermal conductive filler, 5 micron alumina small particle size thermal conductive filler 25 parts, glass fiber 25 parts, coupling agent 0.5 parts, lubricant 0.5 parts. Its preparation method is identical with embodiment one.
PUM
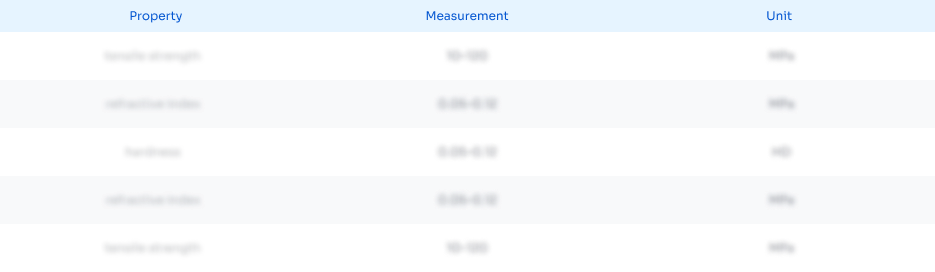
Abstract
Description
Claims
Application Information

- Generate Ideas
- Intellectual Property
- Life Sciences
- Materials
- Tech Scout
- Unparalleled Data Quality
- Higher Quality Content
- 60% Fewer Hallucinations
Browse by: Latest US Patents, China's latest patents, Technical Efficacy Thesaurus, Application Domain, Technology Topic, Popular Technical Reports.
© 2025 PatSnap. All rights reserved.Legal|Privacy policy|Modern Slavery Act Transparency Statement|Sitemap|About US| Contact US: help@patsnap.com