Durable silicon steel furnace bottom roller sleeve and preparation method thereof
A hearth roller and durable technology, applied in the field of durable silicon steel hearth roller sleeve and its preparation, can solve the problems of loose surface of carbonaceous hearth roller sleeve, affecting the quality of silicon steel plate, shortening the service life, etc. The effect of improving oxidation resistance, enhancing wear resistance and prolonging service life
- Summary
- Abstract
- Description
- Claims
- Application Information
AI Technical Summary
Problems solved by technology
Method used
Examples
Embodiment 1
[0013] A durable silicon steel hearth roller casing and a preparation method thereof. Mix 2-6wt% large particles of dense carbonaceous raw materials, 6-10wt% small particles of dense carbonaceous raw materials, 85-90wt% fine powders of dense carbonaceous raw materials and 1.2-1.6wt% Si micropowder, and add the above compounding A mixture of 8-12wt% asphalt powder and phenolic resin is mixed and milled for 20-30 minutes.
[0014] The preparation process of this embodiment is: first press the mixed material after mixing and milling into a silicon steel hearth roller casing blank, and then heat the silicon steel bottom roller casing blank at 1400-1420°C for 6-8 hours Roasting; then put it in a sealed pressure vessel, keep it for 20-30 minutes under the condition of vacuum degree of 10000-1500Pa, then open the valve and inject tar until the tube blank is completely soaked, then evacuate until the vacuum degree is 10000-15000Pa, keep 20 to 30 minutes; finally, keep warm for 8 to 1...
Embodiment 2
[0016] A durable silicon steel hearth roller casing and a preparation method thereof. Mix 6-10wt% large particles of dense carbonaceous raw materials, 6-10wt% small particles of dense carbonaceous raw materials, 80-85wt% fine powder of dense carbonaceous raw materials and 1.6-2.0wt% Si micropowder, and add the above-mentioned A mixture of 12-15wt% asphalt powder and phenolic resin is mixed and milled for 20-30 minutes.
[0017] The preparation process of this embodiment is: first press the mixed material after mixing and milling into a silicon steel hearth roller casing blank, and then heat the silicon steel bottom roller casing blank at 1410-1430°C for 6-8 hours Roasting; then put it in a sealed pressure vessel, keep it for 20-30 minutes under the condition of vacuum degree of 11000-15000Pa, then open the valve and inject tar until the tube blank is completely soaked, then evacuate until the vacuum degree is 11000-15000Pa, keep 20 to 30 minutes; finally, keep warm for 8 to 1...
Embodiment 3
[0019] A durable silicon steel hearth roller casing and a preparation method thereof. Mix 2-6wt% large particles of dense carbonaceous raw materials, 2-6wt% small particles of dense carbonaceous raw materials, 90-95wt% fine powder of dense carbonaceous raw materials and 0.3-0.8wt% Si micropowder, and add the above-mentioned A mixture of 15-20wt% asphalt powder and phenolic resin is mixed and milled for 20-30 minutes.
[0020] The preparation process of this embodiment is: first press the mixed material after mixing and milling into a silicon steel hearth roller sleeve tube billet, and then heat the silicon steel furnace bottom roll sleeve tube billet at 1420-1440 °C for 5-7 hours Roasting; then put it in a sealed pressure vessel, keep it for 18-28 minutes under the condition of vacuum degree of 12000-18000Pa, then open the valve and inject tar until the tube blank is completely soaked, then evacuate until the vacuum degree is 12000-18000Pa, keep 18 to 28 minutes; finally, kee...
PUM
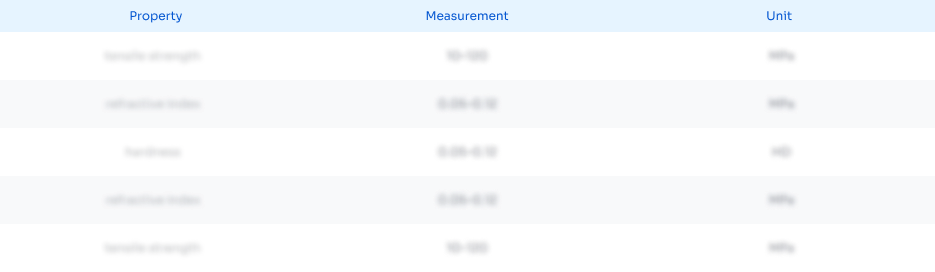
Abstract
Description
Claims
Application Information

- R&D
- Intellectual Property
- Life Sciences
- Materials
- Tech Scout
- Unparalleled Data Quality
- Higher Quality Content
- 60% Fewer Hallucinations
Browse by: Latest US Patents, China's latest patents, Technical Efficacy Thesaurus, Application Domain, Technology Topic, Popular Technical Reports.
© 2025 PatSnap. All rights reserved.Legal|Privacy policy|Modern Slavery Act Transparency Statement|Sitemap|About US| Contact US: help@patsnap.com