Positive pressure thermoforming manufacturing method of wafer-level glass micro-channel
A manufacturing method and glass micro technology, which are applied in the manufacture of microstructure devices, microstructure technology, microstructure devices, etc., can solve the problems of high cost, uncontrollable shape of microchannels, shallow channels, etc., and achieve low cost and molding. The effect of high height and simple method
- Summary
- Abstract
- Description
- Claims
- Application Information
AI Technical Summary
Problems solved by technology
Method used
Image
Examples
Embodiment 1
[0027] A positive pressure thermoforming manufacturing method for a wafer-level glass microchannel, comprising the following steps:
[0028] The first step is to use the Si micromachining process to etch the microfluidic shallow groove pattern on the Si wafer (such as a 4-inch wafer). The silicon wafer used can be a silicon wafer with a standard thickness, such as a 500 micron thick silicon wafer. The depth of the shallow groove is 10-200 microns, such as 15 microns, 30 microns, 40 microns, 60 microns, 95 microns, 132 microns, 150 microns, 180 microns, and the aspect ratio is usually less than 2, such as 1.5, 1, 0.8, 0.5, 0.2, 0.1, 0.05, 0.02, the micromachining process of the pattern structure on the Si wafer is a wet etching process, or a dry inductively coupled plasma (ICP) etching process, reactive ion etching One of them, preferably a wet etching process (lower cost), such as etching with a TMAH solution, the pattern can be striped or serpentine, and can be adjusted as ne...
Embodiment 2
[0035] A positive pressure thermoforming manufacturing method for a wafer-level glass microchannel, comprising the following steps:
[0036] The first step is to use Si micromachining technology to etch microchannel shallow grooves on a 4-inch Si wafer. The silicon wafer used can be a silicon wafer with a standard thickness and a thickness of 500 microns. The depth of the shallow grooves is 60 microns. The runner groove is a strip groove with a diameter of 2 mm, and the length of the groove is 3 cm. The micromachining process of the pattern structure on the Si wafer is a wet etching process, and the used etching solution is a TMAH solution with a concentration of 10% and a temperature of 80 degrees Celsius,
[0037] In the second step, chemically pure calcium carbonate powder is placed in a shallow tank with a particle size of 5 microns and a mass of 30 micrograms.
[0038] The 3rd step, above-mentioned Si disc and Pyrex7740 glass disc (a kind of brand of borosilicate glass, ...
Embodiment 3
[0042] A positive pressure thermoforming manufacturing method for a wafer-level glass microchannel, comprising the following steps:
[0043] The first step is to use Si micromachining technology to etch microchannel shallow grooves on a 4-inch Si wafer. The silicon wafer used can be a silicon wafer with a standard thickness and a thickness of 500 microns. The depth of the shallow grooves is 100 microns. The groove is a strip-shaped groove with a diameter of 1 mm and a length of 2 cm. The micromachining process of the pattern structure on the Si wafer is a wet etching process. The etching solution used is a TMAH solution with a concentration of 10% and a temperature of 80 degrees Celsius. ,
[0044] In the second step, titanium hydride is placed in a shallow tank, the powder particle size is 5 microns, and the mass is 25 micrograms. The high-temperature air release agent can also be preferably pretreated titanium hydride, and the titanium hydride is pretreated in the air at 400...
PUM
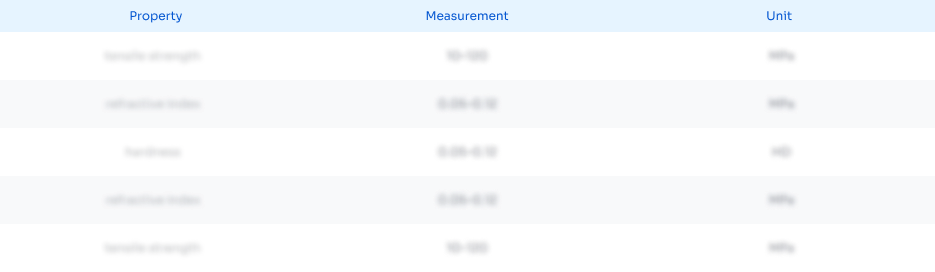
Abstract
Description
Claims
Application Information

- R&D
- Intellectual Property
- Life Sciences
- Materials
- Tech Scout
- Unparalleled Data Quality
- Higher Quality Content
- 60% Fewer Hallucinations
Browse by: Latest US Patents, China's latest patents, Technical Efficacy Thesaurus, Application Domain, Technology Topic, Popular Technical Reports.
© 2025 PatSnap. All rights reserved.Legal|Privacy policy|Modern Slavery Act Transparency Statement|Sitemap|About US| Contact US: help@patsnap.com