Green luminescent material and preparation method thereof
A luminescent material and green technology, applied in the field of green luminescent materials and their preparation, can solve the problems of long afterglow time, unfavorable dynamic picture display, decrease in luminous intensity, etc., and achieve improved luminous performance, good vacuum ultraviolet absorption capacity, good luminous intensity Effect
- Summary
- Abstract
- Description
- Claims
- Application Information
AI Technical Summary
Problems solved by technology
Method used
Image
Examples
Embodiment 1
[0030] Example 1Ca 0.76 Gd 0.02 Tb 0.10 Na 0.12 Al 2 B 2 o 7 Green luminescent material
[0031] Weigh calcium carbonate CaCO 3 0.3803g, aluminum hydroxide Al(OH) 3 0.7800g, boric acid H 3 BO 3 0.7419g (20% excess), sodium carbonate Na 2 CO 3 0.0318g, terbium oxide Tb 4 o 7 0.0934g and gadolinium oxide Gd 2 o 3 0.0181g. After fully grinding all the above-mentioned raw materials in an agate mortar, put them into a corundum crucible for pre-sintering at 500°C for 2 hours, then cool naturally to room temperature, and grind again. Finally, at a volume ratio of 95:5 N 2 and H 2 In the reducing atmosphere formed by the mixed gas, the fully ground pre-sintered product was calcined at 900 ° C for 10 h, cooled naturally to room temperature, and white powder Ca was obtained after grinding. 0.76 Gd 0.02 Tb 0.10 Na 0.12 Al 2 B 2 o 7 Green luminescent material.
Embodiment 2
[0032] Example 2Sr 0.76 Gd 0.02 Tb 0.10 Na 0.12 Al 2 B 2 o 7 Green luminescent material
[0033] Weigh strontium carbonate SrCO 3 0.5610g, aluminum hydroxide Al(OH) 3 0.7800g, boric acid H 3 BO 3 0.7419g (20% excess), sodium carbonate Na 2 CO 3 0.0318g, terbium oxide Tb 4 o 7 0.0934g and gadolinium oxide Gd 2 o 3 0.0181g. After fully grinding all the above-mentioned raw materials in an agate mortar, put them into a corundum crucible for pre-sintering at 500°C for 2 hours, then cool naturally to room temperature, and grind again. Finally, at a volume ratio of 95:5 N 2 and H 2 In the reducing atmosphere formed by the mixed gas, the fully ground pre-sintered product was calcined at 960 ° C for 10 h, and naturally cooled to room temperature. After grinding, the white powder Sr 0.76 Gd 0.02 Tb 0.10 Na 0.12 Al 2 B 2 o 7 Green luminescent material.
[0034] The Sr prepared in this embodiment 0.76 Gd 0.02 Tb 0.10 Na 0.12 Al 2 B 2 o 7 The emission spect...
Embodiment 3
[0035] Example 3Sr 0.76 Gd 0.02 Tb 0.10 Li 0.12 Al 2 B 2 o 7 Green luminescent material
[0036] Weigh strontium carbonate SrCO 3 0.5610g, aluminum hydroxide Al(OH) 3 0.7800g, boric acid H 3 BO 3 0.7419g (20% excess), lithium carbonate Li 2 CO 3 0.0221g, terbium oxide Tb 4 o 7 0.0934g and gadolinium oxide Gd 2 o 3 0.0181g. After fully grinding all the above-mentioned raw materials in an agate mortar, put them into a corundum crucible for pre-sintering at 500°C for 2 hours, then cool naturally to room temperature, and grind again. Finally, in H 2 In the reducing atmosphere formed, the fully ground pre-sintered product was calcined at 960 °C for 10 h, cooled to room temperature naturally, and white powder Sr was obtained after grinding. 0.76 Gd 0.02 Tb 0.10 Li 0.12 Al 2 B 2 o 7 Green luminescent material.
[0037] The Sr prepared in this embodiment 0.76 Gd 0.02 Tb 0.10 Li 0.12 Al 2 B 2 o 7 The emission spectra of green luminescent materials under ...
PUM
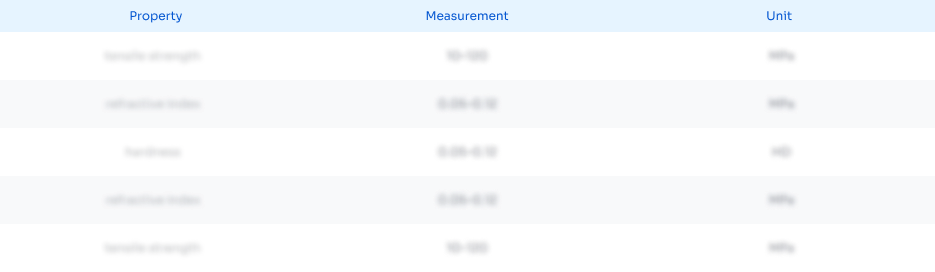
Abstract
Description
Claims
Application Information

- R&D
- Intellectual Property
- Life Sciences
- Materials
- Tech Scout
- Unparalleled Data Quality
- Higher Quality Content
- 60% Fewer Hallucinations
Browse by: Latest US Patents, China's latest patents, Technical Efficacy Thesaurus, Application Domain, Technology Topic, Popular Technical Reports.
© 2025 PatSnap. All rights reserved.Legal|Privacy policy|Modern Slavery Act Transparency Statement|Sitemap|About US| Contact US: help@patsnap.com