Method for preparing thermosetting plastic with coal gangue modified phenolic resin
A technology of phenolic resin and coal gangue, which is applied in the field of three wastes treatment and plastic manufacturing, to achieve the effect of improving strength and toughness, benefiting environmental protection, and improving interface bonding force
- Summary
- Abstract
- Description
- Claims
- Application Information
AI Technical Summary
Problems solved by technology
Method used
Image
Examples
Embodiment 1
[0038] The coal gangue with an ash content of 72.41% and a fixed carbon content of 13.58% is crushed, ball milled, and treated with a coupling agent KH550 aqueous solution, and the dosage of KH550 is 1.5% of that of the gangue. Then, ventilate and dry for later use.
[0039] Take the processed coal gangue, mix it with phenolic resin according to the mass ratio of 55 / 45, add 15% wood powder of the quality of the mixture of coal gangue and phenolic resin, and add 14% of the quality of the mixture of coal gangue and phenolic resin Butyronitrile rubber. After these materials are mixed, put into the double-roll heating machine, and carry out double-roll heating under the condition of 120°C for 30-60min. Add 3% carbon black and 8% curing agent urotropine after the hot refining material is cooled and pulverized, and put it into the mold after mixing. 10 tons, and the final temperature of the mold is 65 ℃, and the mold is solidified to obtain a phenolic molded plate.
Embodiment 2
[0041] The coal gangue with an ash content of 62.48% and a fixed carbon content of 17.13% was crushed and ball milled, and treated with an aqueous solution of coupling agent B201, the amount of which was 2.0% of that of the coal gangue. . Then, ventilate and dry for later use.
[0042] Get the processed coal gangue and mix it with phenolic resin according to the mass ratio of 55 / 45, add 12% wood powder of the quality of the mixture of coal gangue and phenolic resin, and add 10% of the quality of the mixture of coal gangue and phenolic resin Butyronitrile rubber. After mixing these materials, put them into a kneading heat-refining machine, and carry out heat-refining at 125°C for 30-60min. Add 2% carbon black and 6% curing agent trimethylolphenol after cooling and pulverizing the hot refining material. After mixing, put it into the mold. The phenolic molded board was prepared under the conditions of 10 tons and mold final temperature of 65°C.
Embodiment 3
[0044] The coal gangue with an ash content of 66.63% and a fixed carbon content of 19.44% is crushed and ball-milled with an aqueous solution whose dosage of coupling agent KH550 is 1.5% of that of the gangue. Then, ventilate and dry for later use.
[0045] Get the treated coal gangue and mix it with phenolic resin in a mass ratio of 55 / 45, add 12% wood powder of the quality of the mixture of coal gangue and phenolic resin, and add 6% of the quality of the mixture of coal gangue and phenolic resin Butyronitrile For rubber, mix these materials and add them to the double-roll heat refining machine, and carry out double-roll heat refining at 115°C for 30-60 minutes. After the hot mixing material is cooled and pulverized, add 2% carbon black and 6% curing agent Uro Tropin, mixed and put into a mold, cured and molded under the conditions of upper plate temperature of 105°C, lower plate temperature of 70°C, molding pressure of 10 tons, and mold final temperature of 65°C to obtain a ...
PUM
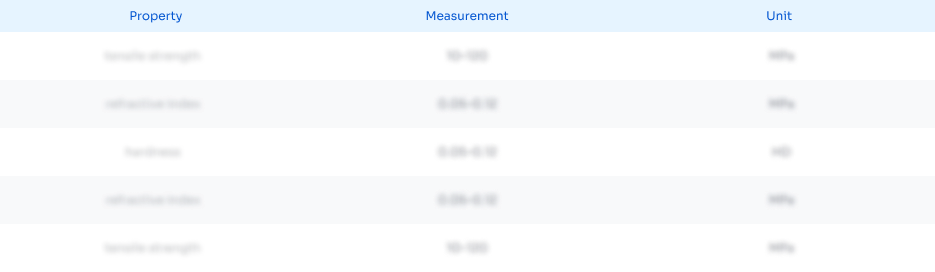
Abstract
Description
Claims
Application Information

- Generate Ideas
- Intellectual Property
- Life Sciences
- Materials
- Tech Scout
- Unparalleled Data Quality
- Higher Quality Content
- 60% Fewer Hallucinations
Browse by: Latest US Patents, China's latest patents, Technical Efficacy Thesaurus, Application Domain, Technology Topic, Popular Technical Reports.
© 2025 PatSnap. All rights reserved.Legal|Privacy policy|Modern Slavery Act Transparency Statement|Sitemap|About US| Contact US: help@patsnap.com