Simple forming process of seal head for titanium alloy cylinder
A forming process, titanium alloy technology, applied in the field of simple forming process of titanium alloy gas cylinder head, can solve the problems of high cost and long production cycle, achieve low cost, increase production cycle, and reduce research and development costs
- Summary
- Abstract
- Description
- Claims
- Application Information
AI Technical Summary
Problems solved by technology
Method used
Image
Examples
Embodiment 1
[0033] The present invention is applied to the TC4 titanium alloy head of Φ89 specification, and the specific implementation method is as follows:
[0034] (1) The wall thickness of the part is 5mm. According to the formula of the technical plan, the wall thickness of the blank is calculated as 10mm, and the gap between the punch and die is 11mm.
[0035] (2) Plasma flame cutting is used for blanking, and the size of the titanium alloy sheet blank is Φ140 0 +4 .
[0036] (3) After blanking, the edge is polished to clean the burrs and oxidized areas; the edge is de-slanted, the maximum thickness of the edge is 2mm, and the angle is 8°; the surface of the blank is coated with FR5 glass lubricant.
[0037] (4) Electric furnace heating, stainless steel is placed in the furnace, and the furnace temperature is set to 940±10°C. After the temperature reaches the set temperature, put the billet into the heating furnace, and keep warm for 15 to 40 minutes.
[0038] (5) The mold is pr...
Embodiment 2
[0041] The present invention is applied to the TC4 titanium alloy head of Φ189 specification, and the specific technical scheme is as follows:
[0042] (1) The wall thickness of the part is 5mm. According to the formula of the technical plan, the wall thickness of the blank is calculated as 10mm, and the gap between the punch and die is 11mm.
[0043] (2) Plasma flame cutting is used for blanking, and the size of the titanium alloy sheet blank is Φ305 0 +4 .
[0044] (3) After blanking, the edge is polished to clean the burrs and oxidized areas; the edge is de-slanted, the maximum thickness of the edge is 2mm, and the angle is 8°; the surface of the blank is coated with FR5 glass lubricant.
[0045] (4) Electric furnace heating, place stainless steel in the furnace, heat to 940±10°C, after the temperature reaches the set temperature, put the billet into the heating furnace, and keep warm for 15-40 minutes.
[0046](5) The mold is preheated to 300±20°C. During the first test...
Embodiment 3
[0049] The present invention is applied to the TA2 titanium alloy head of Φ124 specification, and the specific technical scheme is as follows:
[0050] (1) The wall thickness of this specification part is 6.5mm, the blank wall thickness calculated according to the formula of the technical plan is 12mm, and the gap between the punch and die is 13.2mm.
[0051] (2) Plasma flame cutting is used for blanking, and the size of the titanium alloy sheet blank is Φ200 0 +4 .
[0052] (3) After blanking, the edge is polished to clean burrs and oxidized areas; the edge is de-slanted, the maximum thickness of the edge is 2.4mm, and the angle is 5°; the surface of the blank is coated with FR5 glass lubricant.
[0053] (4) Heating in an electric furnace, place a stainless steel pad in the furnace, heat to 880±10°C, put it into the furnace when it reaches the temperature, and keep it warm for 15 to 40 minutes.
[0054] (5) The mold is preheated to 300±20°C. During the first test, a laser ...
PUM
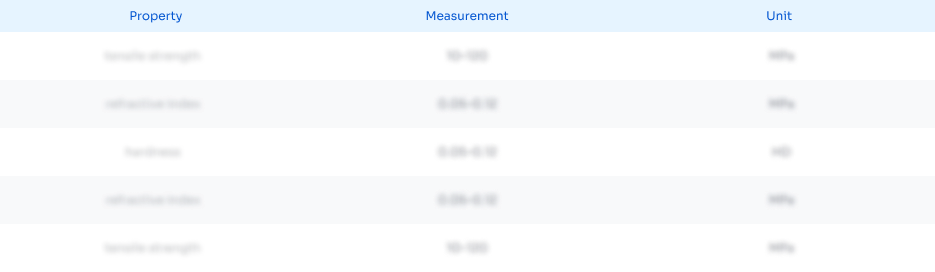
Abstract
Description
Claims
Application Information

- R&D
- Intellectual Property
- Life Sciences
- Materials
- Tech Scout
- Unparalleled Data Quality
- Higher Quality Content
- 60% Fewer Hallucinations
Browse by: Latest US Patents, China's latest patents, Technical Efficacy Thesaurus, Application Domain, Technology Topic, Popular Technical Reports.
© 2025 PatSnap. All rights reserved.Legal|Privacy policy|Modern Slavery Act Transparency Statement|Sitemap|About US| Contact US: help@patsnap.com