Protective film forming method and apparatus
A technology of covering device and film, which is applied in the manufacture of devices, electrical components, and semiconductor/solid-state devices that apply liquid to the surface. The amount of use, good affinity, and the effect of increasing the ratio
- Summary
- Abstract
- Description
- Claims
- Application Information
AI Technical Summary
Problems solved by technology
Method used
Image
Examples
Embodiment Construction
[0032] Hereinafter, preferred embodiments of the protective film covering method and protective film covering apparatus according to the present invention will be described in detail with reference to the accompanying drawings.
[0033] exist figure 1 , shows a perspective view of a laser processing machine equipped with a protective film covering device according to the present invention.
[0034] figure 1 The laser processing machine shown has an approximately cuboid housing 2 . In the casing 2 of this device, a chuck table 3 as a workpiece holding unit for holding a workpiece is disposed so as to be movable in a direction indicated by an arrow X which is a machining feeding direction. The chuck table 3 has a suction chuck support base 31 and a suction chuck 32 mounted on the suction chuck support base 31, and sucks, for example, a disc-shaped semiconductor to be processed by a suction unit not shown. The wafer is held on the surface of the suction chuck 32 , that is, the m...
PUM
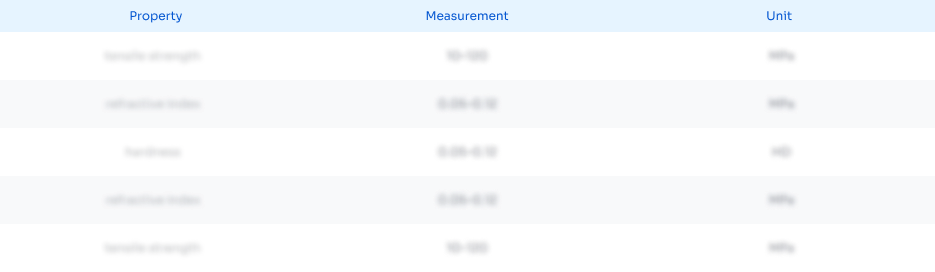
Abstract
Description
Claims
Application Information

- R&D
- Intellectual Property
- Life Sciences
- Materials
- Tech Scout
- Unparalleled Data Quality
- Higher Quality Content
- 60% Fewer Hallucinations
Browse by: Latest US Patents, China's latest patents, Technical Efficacy Thesaurus, Application Domain, Technology Topic, Popular Technical Reports.
© 2025 PatSnap. All rights reserved.Legal|Privacy policy|Modern Slavery Act Transparency Statement|Sitemap|About US| Contact US: help@patsnap.com