Semi-wet slag treatment waste heat recovery generating system and method
A waste heat recovery system and waste heat recovery technology, which are applied in heat recovery systems, steam generation methods using heat carriers, waste gas treatment, etc., can solve the problems of poor production stability, low product quality, and low utilization efficiency, and prevent slag The effect of clogging, high vitreous content and easy maintenance and repair
- Summary
- Abstract
- Description
- Claims
- Application Information
AI Technical Summary
Problems solved by technology
Method used
Image
Examples
Embodiment Construction
[0049] The present invention proposes a semi-wet slag treatment waste heat recovery power generation system, which includes a semi-wet slag treatment system, a waste heat recovery system and a waste heat power generation system, wherein the semi-wet slag treatment system utilizes high-pressure water mist or gas mist ( The following uses high-pressure gas mist as an example to illustrate) to cool the blast furnace liquid slag, and use the crushing device to mechanically crush the slag, and process it into raw materials for making cement; The waste heat is recovered and stored in the thermal energy storage system; the waste heat power generation system converts the thermal energy in the thermal energy storage system into power mechanical energy, and drives the generator to convert the mechanical energy into electrical energy.
[0050] figure 1 It is a schematic diagram of the structure and treatment method flow chart of a specific embodiment of the semi-wet slag treatment waste ...
PUM
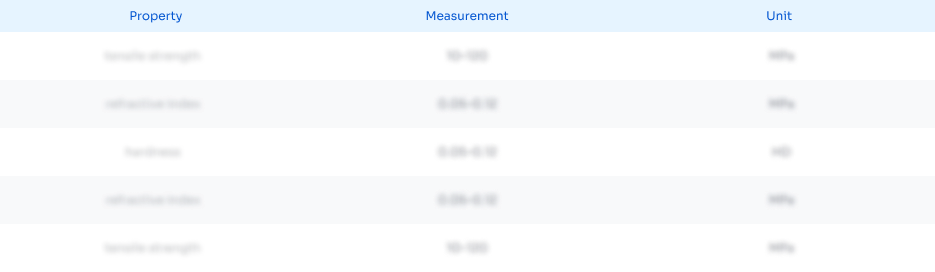
Abstract
Description
Claims
Application Information

- Generate Ideas
- Intellectual Property
- Life Sciences
- Materials
- Tech Scout
- Unparalleled Data Quality
- Higher Quality Content
- 60% Fewer Hallucinations
Browse by: Latest US Patents, China's latest patents, Technical Efficacy Thesaurus, Application Domain, Technology Topic, Popular Technical Reports.
© 2025 PatSnap. All rights reserved.Legal|Privacy policy|Modern Slavery Act Transparency Statement|Sitemap|About US| Contact US: help@patsnap.com