Coal water slurry additive and preparation method and application thereof
A technology of coal water slurry and additives, applied in fuel, liquid carbon-containing fuel, petroleum industry, etc., can solve the problems of high cost and narrow range of coal types, achieve the effect of less dosage, best effect, and lower use cost
- Summary
- Abstract
- Description
- Claims
- Application Information
AI Technical Summary
Problems solved by technology
Method used
Examples
Embodiment 1
[0015] Put the four-neck flask equipped with electric stirring, condenser, addition funnel and thermometer on the oil bath. Weigh 1.0 moles of industrially purified washing oil (coal tar boiling range 230~300°C fraction, the main components are methylnaphthalene, biphenyl, indole, acenaphthene, etc. Wherein, the phenol content is not more than 0.5%, and the naphthalene content Not more than 15%, moisture not more than 1.0%) into the four-necked flask. At 145°C, 1.65 mol of sulfuric acid was added and reacted for 4 hours. After the sulfonation is complete, cool down. At 80° C., 0.2 mol of p-aminobenzenesulfonic acid, 0.2 mol of phenol and 0.85 mol of formaldehyde were added, and kept at 95° C. for 3 hours. After polycondensation, neutralize with sodium hydroxide until the pH value is 8.0, put it into an oven for drying, take it out after drying, grind it into powder while it is hot, and obtain sample 1#.
[0016] Use sample 1# to do the slurrying test, the test steps are as ...
Embodiment 2
[0021] Put the four-neck flask equipped with electric stirring, condenser, addition funnel and thermometer on the oil bath. Weigh 1.0 mole of industrially purified washing oil and put it into a four-necked flask. Add 1.5 mole of sulfuric acid at 120°C for 3 hours. After the sulfonation is complete, cool down. At 80°C, 0.1 mole of sodium diaminobenzenesulfonate, 0.1 mole of resorcinol and 0.7 mole of formaldehyde were added, and kept at 80°C for 2 hours. After the polycondensation, it was neutralized with ammonia water until the pH value was 7.0, put into an oven for drying, and after drying, it was taken out while hot and ground into powder to obtain sample 2#.
[0022] Sample 2# was used for pulping test, and the results are shown in Table 2.
[0023] Table 2, 2# additive sample pulping test results
[0024] coal type
[0025] Explanation: It can be seen from Table 2 that under the conditions of Example 2, the highest slurry concentrations of the four kinds of c...
Embodiment 3
[0027] Put the four-neck flask equipped with electric stirring, condenser, addition funnel and thermometer on the oil bath. Weigh 1.0 mole of industrially purified washing oil and put it into a four-necked flask. At 170°C, 1.8 moles of sulfuric acid was added to react for 5 hours. After the sulfonation is complete, cool down. At 80°C, 0.3 mole of sodium methylaminobenzenesulfonate, 0.3 mole of bisphenol A and 1.0 mole of formaldehyde were added, and kept at 110°C for 4 hours. After polycondensation, neutralize with potassium hydroxide to a pH value of 9.0, put it in an oven for drying, take it out after drying, and grind it into powder while it is hot to obtain sample 3#.
[0028] Sample 3# was used for pulping test, and the results are shown in Table 3.
[0029] Table 3. Pulping test results of 3# additive samples
[0030] coal type
[0031] Explanation: It can be seen from Table 3 that under the conditions of Example 3, the highest slurry concentrations of the ...
PUM
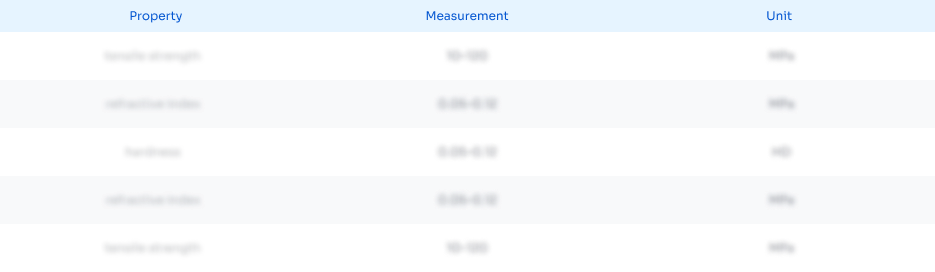
Abstract
Description
Claims
Application Information

- R&D
- Intellectual Property
- Life Sciences
- Materials
- Tech Scout
- Unparalleled Data Quality
- Higher Quality Content
- 60% Fewer Hallucinations
Browse by: Latest US Patents, China's latest patents, Technical Efficacy Thesaurus, Application Domain, Technology Topic, Popular Technical Reports.
© 2025 PatSnap. All rights reserved.Legal|Privacy policy|Modern Slavery Act Transparency Statement|Sitemap|About US| Contact US: help@patsnap.com