Preparation method of Si3N4-SiC-C fire-resistant material powder
A technology of si3n4-sic-c and refractory raw materials, which is applied in the field of preparing Si3N4-SiC-C refractory raw materials, can solve the problems of high price, complicated preparation process and large power consumption, and achieves low cost, simple equipment and energy consumption. less effect
- Summary
- Abstract
- Description
- Claims
- Application Information
AI Technical Summary
Problems solved by technology
Method used
Examples
Embodiment 1
[0018] Raw materials and ratio:
[0019] The addition of quartz powder is 71.4wt%, of which SiO 2 The content percentage is 98.0%, and the average particle size is less than 0.074mm; the coke powder addition is 28.6wt%, and the C content percentage is 90.0%, and the average particle size is less than 0.150mm. The addition amount of the external binder (silica sol) is 2-3% of the total batching mass.
[0020] Ingredients, mix:
[0021] First, various raw materials are loaded into a mixer according to the above proportions, and dry ball milled for 10 hours to fully mix the raw materials evenly, the particle size is less than 0.150mm, and the sieve residue of the aperture is less than 2.0wt%.
[0022] Shaped or balled:
[0023] Put the raw materials mixed by ball mill into the mixer, add appropriate amount of water and mix them, and then shape the materials into green bodies on the molding machine (or shape them into spherical particles with a ball forming machine).
[0024] ...
Embodiment 2
[0030] Raw materials and ratio:
[0031] The amount of silica fume added is 62.5wt%, of which SiO 2 The content percentage is 92.0%, and the average particle size is less than 0.074mm; the addition amount of graphite electrode powder is 37.5wt%, and the C content percentage is 90.0%, and the average particle size is less than 0.150mm. The addition amount of the external binding agent (polyvinyl alcohol) is 2-3% of the total batching quality.
[0032] Ingredients, mix:
[0033] Firstly, various raw materials are loaded into a mixer according to the above ratio, and dry ball milled for 8 hours to fully mix the raw materials evenly, the particle size is less than 0.150mm, and the sieve residue of the aperture is less than 2.0wt%.
[0034] Shaped or balled:
[0035] Put the raw materials mixed by ball mill into the mixer, add appropriate amount of water and mix them, and then shape the materials into green bodies in the molding machine (or shape them into spherical particles wi...
Embodiment 3
[0042] Raw materials and ratio:
[0043] The amount of silica fume added is 32.5wt%, of which SiO 2 The content percentage is 92.0%, and the average particle size is less than 0.074mm; the addition of quartz powder is 31.4wt%, of which SiO 2 The content percentage is 98.0%, and the average particle size is less than 0.074mm; the addition amount of coke powder is 18.6wt%, and the C content percentage is 90.0%, and the average particle size is less than 0.150mm. The addition amount of graphite electrode powder is 17.5wt%, wherein the percentage of C content is 90.0%, and the average particle size is less than 0.150mm. The addition amount of the external binding agent (polyvinyl alcohol) is 2-3% of the total batching quality.
[0044] Ingredients, mix:
[0045] First, various raw materials are loaded into a mixer according to the above proportions, and dry ball milled for 12 hours to fully mix the raw materials evenly, the particle size is less than 0.100mm, and the sieve resi...
PUM
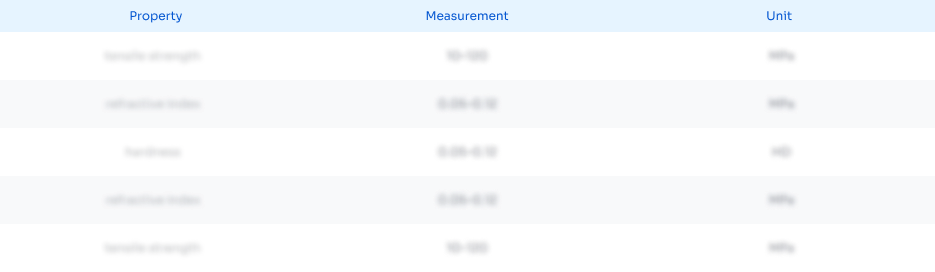
Abstract
Description
Claims
Application Information

- R&D Engineer
- R&D Manager
- IP Professional
- Industry Leading Data Capabilities
- Powerful AI technology
- Patent DNA Extraction
Browse by: Latest US Patents, China's latest patents, Technical Efficacy Thesaurus, Application Domain, Technology Topic, Popular Technical Reports.
© 2024 PatSnap. All rights reserved.Legal|Privacy policy|Modern Slavery Act Transparency Statement|Sitemap|About US| Contact US: help@patsnap.com