Method for detoxifying chromium slags
A technology of chromium slag and walnut shell, applied in the direction of protection device against harmful chemicals, can solve the problems of increased production cost, increased production cost, increased operation difficulty, etc. Effect
- Summary
- Abstract
- Description
- Claims
- Application Information
AI Technical Summary
Problems solved by technology
Method used
Image
Examples
Embodiment 1
[0041]Put 10g of chromium slag and 1.0g of walnut shell into the ceramic crucible, and mix evenly, then put the reactor into the microwave oven, use slag wool insulation material around the reactor to keep warm, and use a shielded armored thermocouple to measure the microwave field. Temperature: raise the temperature to 700°C, keep warm for 20 minutes, turn off the microwave oven, open the furnace door after 5 minutes, immerse the material in distilled water after the material is cooled, filter after soaking for 24 hours, and dilute the filtrate to 250ml, use diphenylcarbazide Determination of Cr in filtrate by spectrophotometry 6+ Concentration, calculated as Cr 6+ The detoxification rate is 99.012%.
Embodiment 2
[0043] Put 10g of chromium slag and 2.0g of walnut shell into the ceramic crucible, and mix evenly, then put the reactor into the microwave oven, use slag wool insulation material around the reactor to keep warm, and use a shielded armored thermocouple to measure the microwave field. temperature, raise the temperature to 800°C, keep warm for 15 minutes, then close the microwave oven, and open the furnace door after 5 minutes. After the material is cooled, immerse the material in distilled water, filter after soaking for 24 hours, and dilute the filtrate to 250ml. Determination of Cr in filtrate by spectrophotometry 6+ Concentration, calculated as Cr 6+ The detoxification rate is 99.117%.
Embodiment 3
[0045] Put 10g of chromium slag and 5.0g of walnut shell into the ceramic crucible, and mix evenly, then put the reactor into the microwave oven, keep warm with slag wool insulation material around the reactor, and use a shielded armored thermocouple to measure the microwave field Temperature, raise the temperature to 900°C, keep warm for 10 minutes, turn off the microwave oven, open the furnace door after 5 minutes, immerse the material in distilled water after the material is cooled, filter after soaking for 24 hours, and dilute the filtrate to 250ml. Determination of Cr in filtrate by spectrophotometry 6+ Concentration, calculated as Cr 6+ The detoxification rate is 99.258%.
PUM
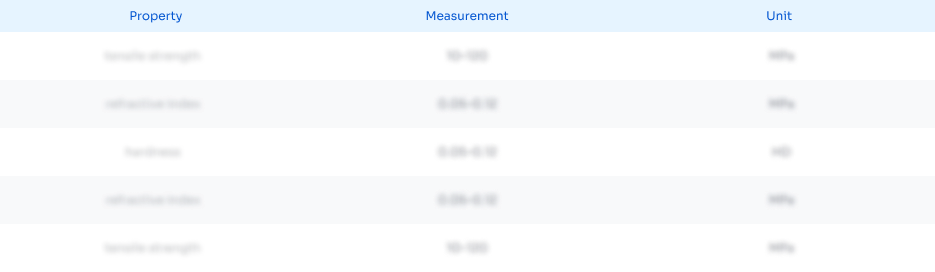
Abstract
Description
Claims
Application Information

- Generate Ideas
- Intellectual Property
- Life Sciences
- Materials
- Tech Scout
- Unparalleled Data Quality
- Higher Quality Content
- 60% Fewer Hallucinations
Browse by: Latest US Patents, China's latest patents, Technical Efficacy Thesaurus, Application Domain, Technology Topic, Popular Technical Reports.
© 2025 PatSnap. All rights reserved.Legal|Privacy policy|Modern Slavery Act Transparency Statement|Sitemap|About US| Contact US: help@patsnap.com