Method for manufacturing polycrystalline silicon by reducing silicon chloride with active metal
A technology of active metals and chlorides, applied in silicon compounds, chemical instruments and methods, non-metallic elements, etc., can solve the problems that cannot be directly used to make solar cells, consume large power, limit production, etc., and achieve easy control and recycling Utilization, less environmental pollution and lower energy consumption
- Summary
- Abstract
- Description
- Claims
- Application Information
AI Technical Summary
Problems solved by technology
Method used
Image
Examples
Embodiment Construction
[0015] Refer to attached figure 1 , with figure 1 It is a schematic diagram of the operation flow of an embodiment of a method for producing polysilicon by using active metals to reduce silicon chlorides to produce polysilicon provided by the present invention: perform silicon reduction on trichlorosilane purified by rectification and magnesium metal purified by vacuum distillation After the reaction, the mixture after the reduction reaction is washed with high-purity water and acid, and then filtered, and the magnesium chloride and unreacted trichlorosilane are separated to check that there is no magnesium chloride or trichlorohydrogen After silicon, stop cleaning; filter to obtain silicon powder product. The silicon powder is dried in a vacuum oven, and the dried silicon is distilled in a vacuum distillation device or rectified in a vacuum rectification device to obtain high-purity polysilicon products.
PUM
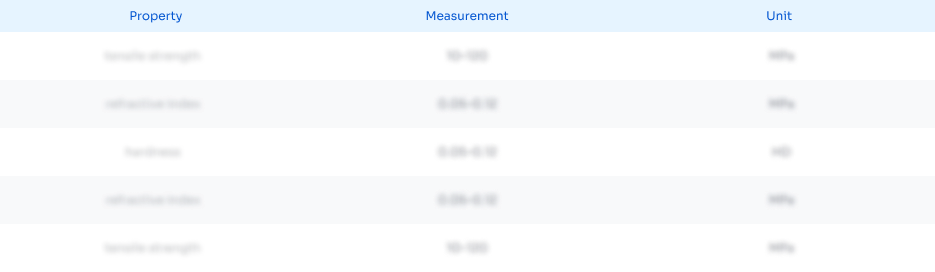
Abstract
Description
Claims
Application Information

- R&D Engineer
- R&D Manager
- IP Professional
- Industry Leading Data Capabilities
- Powerful AI technology
- Patent DNA Extraction
Browse by: Latest US Patents, China's latest patents, Technical Efficacy Thesaurus, Application Domain, Technology Topic, Popular Technical Reports.
© 2024 PatSnap. All rights reserved.Legal|Privacy policy|Modern Slavery Act Transparency Statement|Sitemap|About US| Contact US: help@patsnap.com