Method and device for soft stop control for pump loaded motor
A control method and technology for pump loads, applied in motor generator control, AC motor control, control systems, etc., can solve problems such as pump load surge and pump load, improve stability and solve pump load surge The effect of vibration and descent is stable
- Summary
- Abstract
- Description
- Claims
- Application Information
AI Technical Summary
Problems solved by technology
Method used
Image
Examples
Embodiment 1
[0044] Embodiment 1: In order to solve the above technical problems, a soft stop control method of a pump load motor in the present invention includes the following steps:
[0045] 1.1. After entering the soft stop process, connect the working voltage to the main circuit and then output to the motor;
[0046]1.2. Control the conduction angle of the thyristor of the main circuit according to the predetermined motor voltage drop curve;
[0047] 1.3. Collect the voltage and current output from the main circuit to the motor;
[0048] 1.4. Set the voltage and current according to or Establish a mathematical model to calculate the real-time active power of the motor; for a single-phase AC asynchronous motor, the average active power consumed in one cycle can be defined as:
[0049] P = ∫ t 0 t 0 + ...
Embodiment 2
[0065] Embodiment 2: In the process of reducing the motor speed, due to the inherent characteristics of the asynchronous motor, when the load is large, the peak current of the motor can reach several times of the rated current. This situation is undesirable. Therefore, on the basis of active power closed-loop control, it is also necessary to add current limiting to ensure that the motor current will not exceed the allowable current value during the soft stop process.
[0066] In order to increase the current limiting control, the real-time active power is compared with the predetermined active power, and the current difference between the two is obtained as the predetermined current, which is compared with the motor current obtained by sampling to generate a current error signal, which is used by the current PID regulator This current error signal is used as an input to control the phase shift angle of the main circuit.
[0067] A soft stop control method for a pump load moto...
PUM
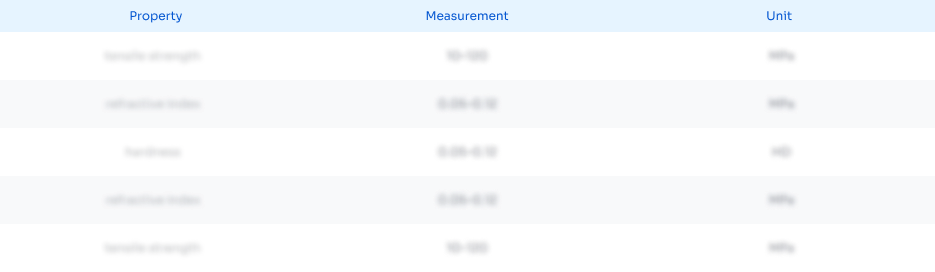
Abstract
Description
Claims
Application Information

- R&D
- Intellectual Property
- Life Sciences
- Materials
- Tech Scout
- Unparalleled Data Quality
- Higher Quality Content
- 60% Fewer Hallucinations
Browse by: Latest US Patents, China's latest patents, Technical Efficacy Thesaurus, Application Domain, Technology Topic, Popular Technical Reports.
© 2025 PatSnap. All rights reserved.Legal|Privacy policy|Modern Slavery Act Transparency Statement|Sitemap|About US| Contact US: help@patsnap.com