Method and device for extracting iron from melted reduced nickel slag
A technology of nickel slag and melting section, which is applied in the field of resource utilization and waste heat recovery, can solve the problem of unreliable nickel slag, and achieve the effect of simple structure, less equipment investment and zero emission
- Summary
- Abstract
- Description
- Claims
- Application Information
AI Technical Summary
Problems solved by technology
Method used
Image
Examples
Embodiment 1
[0024] A method for extracting iron from smelting reduced nickel slag. The hot nickel slag and a small amount of cold slag are placed in an electric furnace and energized to raise the temperature. When the temperature reaches 1500-1550°C, a slagging agent, a reducing agent and other auxiliary materials are added. The stirring effect of the spray gun makes the reducing agent react with FeO in the slag to generate metallic iron and carbon monoxide. This method simultaneously completes two processes of nickel slag melting and reduction on an electric furnace, heats in the electric furnace, melts to a molten state, flows from the melting section into the reduction section, forms a certain molten pool in the reduction section, and gradually sprays coal powder into the nickel slag. The iron in the slag is reduced, and at the same time, lime and other auxiliary materials are added for slagging, that is, the iron in the nickel slag is reduced.
[0025] After a period of reduction reac...
Embodiment 2
[0031] For each ton of nickel slag raw material, the proportions by weight of coal powder, lime powder, and other auxiliary materials are as follows: coal powder 0.3t, lime powder 0.7t, bauxite 0.24t, iron sheet 0.005t, scrap steel 0.085t, fluorite 0.88 t. All the other techniques and contents are the same as in Example 1.
Embodiment 3
[0033] For each ton of nickel slag raw material, the proportions by weight of coal powder, lime powder, and other auxiliary materials are as follows: coal powder 0.15t, lime powder 0.56t, bauxite 0.1t, iron sheet 0.002t, scrap steel 0.06t, fluorite 0.6 t. All the other techniques and contents are the same as in Example 1.
PUM
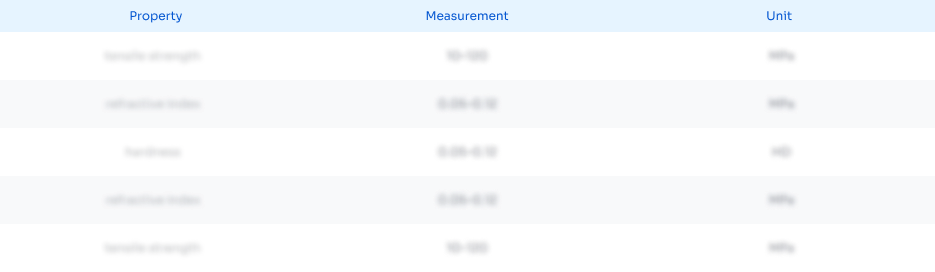
Abstract
Description
Claims
Application Information

- R&D
- Intellectual Property
- Life Sciences
- Materials
- Tech Scout
- Unparalleled Data Quality
- Higher Quality Content
- 60% Fewer Hallucinations
Browse by: Latest US Patents, China's latest patents, Technical Efficacy Thesaurus, Application Domain, Technology Topic, Popular Technical Reports.
© 2025 PatSnap. All rights reserved.Legal|Privacy policy|Modern Slavery Act Transparency Statement|Sitemap|About US| Contact US: help@patsnap.com