Electroless plating method for preparing magnetoelectric composite material
A magnetoelectric composite material and electroless plating technology, applied in liquid chemical plating, metal material coating process, coating and other directions, can solve the problem of reducing the magnetoelectric coefficient of magnetoelectric composite materials, and achieve improved coupling performance and deep plating. Strong ability and uniform coating effect
- Summary
- Abstract
- Description
- Claims
- Application Information
AI Technical Summary
Problems solved by technology
Method used
Image
Examples
Embodiment 1
[0028] Cut the PZT to size 18×5×0.4mm 3 Ultrasonic cleaning of flake samples in a mixed solution of alcohol and acetone for 10 minutes; first put the sample in 0.4M hydrofluoric acid solution to roughen for 2 minutes, take it out and rinse it with distilled water; put the sample in 0.08M hydrofluoric acid solution In stannous solution, sensitize at room temperature for 5 minutes, take it out and rinse with distilled water; put the sample in 0.001M palladium chloride solution, activate it at room temperature for 5 minutes, take it out and rinse with distilled water; finally put the sample in 0.2M The sodium phosphite solution is reduced for 15 seconds, and electroless plating can be performed after rinsing with distilled water.
[0029] First, weigh the reagents required for the chemical plating solution formula, dissolve them and mix them separately, adjust the pH value to 9 with NaOH solution, and then dilute to the specified volume with distilled water; then, heat it to 75°C...
Embodiment 2
[0033] Cut the PZT to size 18×6×0.5mm 3 Ultrasonic cleaning of flake samples in a mixed solution of alcohol and acetone for 10 minutes; first put the sample in 0.65M hydrofluoric acid solution for roughening for 6 minutes, take it out and rinse it with distilled water; put the sample in 0.15M hydrofluoric acid solution In stannous solution, sensitize at room temperature for 30 minutes, rinse with distilled water after taking it out; put the sample in 0.005M palladium chloride solution, activate at room temperature for 30 minutes, take it out and rinse with distilled water; finally put the sample in 0.4M The sodium phosphite solution is reduced for 60 seconds, and electroless plating can be performed after rinsing with distilled water.
[0034]First, weigh the medicines required for the chemical plating solution formula, dissolve them and mix them separately, adjust the pH value to 12.5 with NaOH solution, and then dilute to the specified volume with distilled water; then, heat...
Embodiment 3
[0039] Cut the PZT to size 18×5×0.4mm 3 Ultrasonic cleaning of flake samples in a mixed solution of alcohol and acetone for 10 minutes; first put the sample in 0.4M hydrofluoric acid solution to roughen for 2 minutes, take it out and rinse it with distilled water; put the sample in 0.08M hydrofluoric acid solution In stannous solution, sensitize at room temperature for 5 minutes, take it out and rinse with distilled water; put the sample in 0.001M palladium chloride solution, activate it at room temperature for 5 minutes, take it out and rinse with distilled water; finally put the sample in 0.2M The sodium phosphite solution is reduced for 15 seconds, and electroless plating can be performed after rinsing with distilled water.
[0040] First, weigh the reagents required for the chemical plating solution formula, dissolve them and mix them separately, adjust the pH value to 9 with NaOH solution, and then dilute to the specified volume with distilled water; then, heat it to 75°C...
PUM
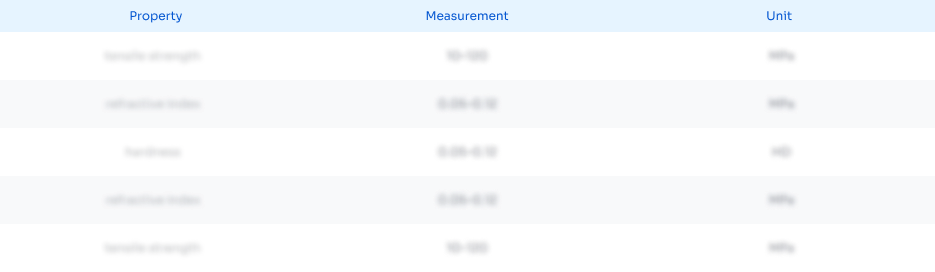
Abstract
Description
Claims
Application Information

- R&D
- Intellectual Property
- Life Sciences
- Materials
- Tech Scout
- Unparalleled Data Quality
- Higher Quality Content
- 60% Fewer Hallucinations
Browse by: Latest US Patents, China's latest patents, Technical Efficacy Thesaurus, Application Domain, Technology Topic, Popular Technical Reports.
© 2025 PatSnap. All rights reserved.Legal|Privacy policy|Modern Slavery Act Transparency Statement|Sitemap|About US| Contact US: help@patsnap.com