Waterborne rust conversion polymer emulsion, coating thereof and method for preparing same
A polymer emulsion, rust-to-rust technology, applied in anti-corrosion coatings, coatings, etc., can solve problems such as poor effect, time-consuming, labor-intensive, etc., achieve less equipment investment, no waste discharge, and reduce construction intensity Effect
- Summary
- Abstract
- Description
- Claims
- Application Information
AI Technical Summary
Problems solved by technology
Method used
Image
Examples
Embodiment 1
[0044] Embodiment 1, the preparation of a kind of water-based rust turning rust polymer emulsion
[0045]
[0046] Preparation:
[0047] 1. Dissolving 2g of ammonium persulfate in deionized water is prepared into a 4% concentration of oxidizing agent aqueous solution for subsequent use; 3g of sodium thiosulfate is dissolved in deionized water and prepared into a 6% concentration of reducing agent aqueous solution for subsequent use;
[0048] 2. In the reactor, add 28Kg deionized water, 0.26Kg sodium secondary alkylbenzene sulfonate, 0.13Kg alkylphenol polyoxyethylene ether OP-35 in the first stage, replace with nitrogen and add 1.35Kg partial Ethylene dichloride, 0.10Kg methyl methacrylate, 0.06Kg acrylic acid mixed monomer, control the stirring speed to 100rpm, stir for 5min and then raise the temperature to 45°C, add the oxidizing agent aqueous solution prepared in the first step, and add the reducing agent aqueous solution dropwise after 15 minutes Carry out polymerizat...
Embodiment 2
[0051] Example 2 Preparation of a water-based polymer emulsion with rust and rust
[0052]
[0053] Preparation:
[0054] 1. Dissolve 2g of sodium persulfate in deionized water and prepare an aqueous solution of 4% concentration of oxidizing agent for subsequent use; dissolve 3g of sodium thiosulfate in deionized water and prepare an aqueous solution of reducing agent with a concentration of 6% for subsequent use;
[0055] 2. In the reactor, add 28Kg deionized water, 0.30Kg NP-40, 0.15Kg Dowfax in the first stage, replace with nitrogen and vacuumize, add 1.4Kg vinyl chloride, 0.03Kg methyl methacrylate, 0.02Kg methacrylic acid Mix the monomers, control the stirring speed to 100rpm, stir for 5 minutes, then raise the temperature to 45°C, add the oxidizing agent aqueous solution prepared in the first step, add the reducing agent aqueous solution dropwise after 15 minutes for polymerization, react for 1-2 hours, and the pressure in the polymerization tank is 0.08- 0.12 MPa. ...
Embodiment 3
[0058] Example 3 Preparation of a water-based polymer emulsion with rust and rust
[0059]
[0060]
[0061] Preparation:
[0062] 1. Dissolve 2g of potassium persulfate in deionized water and prepare an aqueous solution of 4% concentration of oxidizing agent for subsequent use; dissolve 3g of sodium thiosulfate in deionized water and prepare an aqueous solution of reducing agent with a concentration of 6% for subsequent use;
[0063] 2. In the reactor, add 28Kg deionized water and 0.10Kg poly-(oxo-1,2-ethylene dimethylene)-α-nonylphenyl-ω-hydroxyl (NP-40) in the first stage , 0.20Kg alkyl diphenyl oxide disulfonate Dowfax, replace with nitrogen and vacuumize, add 1.3Kg vinylidene chloride, 0.02Kg butyl acrylate and 0.004Kg methacrylic acid mixed monomer, control the stirring speed to 100rpm After stirring for 5 minutes, the temperature was raised to 45°C, and the oxidizing agent aqueous solution prepared in the first step was added. After 15 minutes, the reducing agent...
PUM
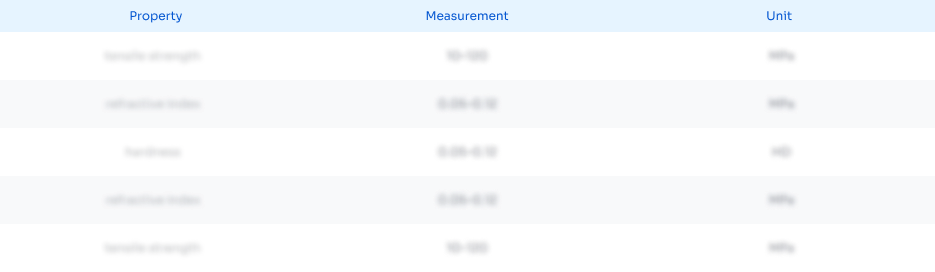
Abstract
Description
Claims
Application Information

- R&D Engineer
- R&D Manager
- IP Professional
- Industry Leading Data Capabilities
- Powerful AI technology
- Patent DNA Extraction
Browse by: Latest US Patents, China's latest patents, Technical Efficacy Thesaurus, Application Domain, Technology Topic, Popular Technical Reports.
© 2024 PatSnap. All rights reserved.Legal|Privacy policy|Modern Slavery Act Transparency Statement|Sitemap|About US| Contact US: help@patsnap.com