Method for preparing cylohexanediol diglycidyl ether
A technology of diglycidyl ether and cyclohexanediol, applied in the direction of organic chemistry, can solve the problems of deepening product color, strong corrosion of equipment, increasing energy consumption, etc., to achieve environmental protection, shorten process time, and save The effect of energy consumption
- Summary
- Abstract
- Description
- Claims
- Application Information
AI Technical Summary
Problems solved by technology
Method used
Examples
Embodiment 1
[0013] Take 1mol epoxycyclohexane, 30mol water, and 0.0002mol fluoroboric acid into the reaction kettle, react between 75°C and 85°C, react until the epoxycyclohexane is completely hydrated, add 3mol of toluene for dehydration, and dehydrate Keep warm at 70°C to 75°C, then add 0.003mol of fluoboric acid, dropwise add 2.5mol of epichlorohydrin, react at 70°C to 75°C for 4 to 6 hours, after the reaction is complete, add 2.55mol of NaOH solution dropwise, drop After the addition, keep it warm at 40°C to 50°C for 4 to 5 hours. After the reaction, separate the oil phase, wash the oil phase with water until neutral, then filter and distill off the light components to obtain the product.
Embodiment 2
[0015] Take 1.5mol of water and 0.01mol of fluoboric acid into the reaction kettle, keep the reaction kettle between 10°C and 20°C and add 1mol of epoxycyclohexane dropwise, and continue the reaction until the epoxycyclohexane is completely hydrated , add 1.5mol of cyclohexane for distillation and dehydration, keep warm at 10°C to 20°C after dehydration, add 2.1mol of epichlorohydrin dropwise, react at 10°C to 20°C for 9 to 10 hours, the reaction is complete, Add 4.15mol Na dropwise 2 CO 3 After the solution is added dropwise, keep it warm at 30°C to 40°C and react for 5 to 6 hours. After the reaction, separate the oil phase, wash the oil phase with water until it is neutral, then filter and distill off the light components to obtain the product.
Embodiment 3
[0017] Take 15mol of water and 0.003mol of fluoroboric acid into the reaction kettle, keep the reaction kettle between 40°C and 50°C and add 1mol of epoxycyclohexane dropwise, after the dropwise addition, continue to react until the epoxycyclohexane is completely hydrated, Add 1.5mol of toluene for distillation and dehydration. After dehydration, continue to keep warm at 50°C-60°C, add 1.8mol of epichlorohydrin dropwise, and react at 50°C-60°C for 4-5 hours. After the reaction is complete, add dropwise 1.85mol NaOH solution, after the dropwise addition, keep it warm at 50°C to 60°C and react for 3 to 4 hours. After the reaction, separate the oil phase, wash the oil phase with water until it is neutral, then filter and distill off the light components to obtain the product.
PUM
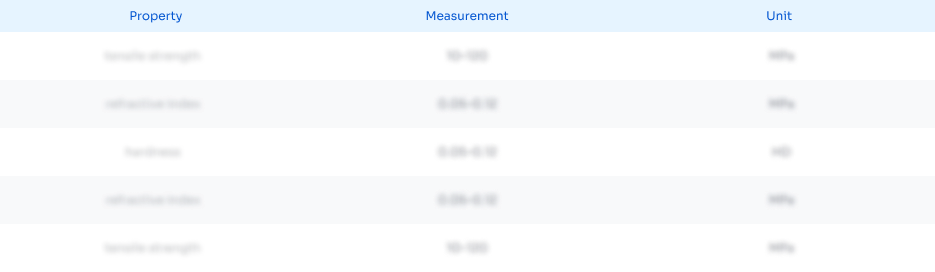
Abstract
Description
Claims
Application Information

- R&D
- Intellectual Property
- Life Sciences
- Materials
- Tech Scout
- Unparalleled Data Quality
- Higher Quality Content
- 60% Fewer Hallucinations
Browse by: Latest US Patents, China's latest patents, Technical Efficacy Thesaurus, Application Domain, Technology Topic, Popular Technical Reports.
© 2025 PatSnap. All rights reserved.Legal|Privacy policy|Modern Slavery Act Transparency Statement|Sitemap|About US| Contact US: help@patsnap.com