Powder metallurgy preparation method for rare-earth containing oxide reinforcing phase titanium alloy
A rare earth oxide, phase titanium alloy technology, applied in the field of titanium alloy processing, can solve problems such as storage and transportation difficulties, and achieve the effects of favorable shape and distribution, simple preparation process, and reduced tonnage
- Summary
- Abstract
- Description
- Claims
- Application Information
AI Technical Summary
Problems solved by technology
Method used
Image
Examples
Embodiment 1
[0019] Weigh Fe: 1.5%, Mo: 2.25%, YH 2 Powder (100 mesh): 0.1%, the rest is hydrogenated dehydrogenation titanium powder, the above powder is fully mixed and pressed into shape, and then the compact is put into a vacuum sintering furnace and sintered at 1300 ° C / 1.5 hours to make a titanium alloy sintered compact . Then the sintered green body was rolled and deformed at 1200°C / 90% high temperature, and its mechanical properties were tested.
Embodiment 2
[0021] Weigh Fe: 1.5%, Mo: 2.25%, YH 2 (100 mesh): 0.6%, the balance is hydrogenated dehydrogenated titanium powder, the above powders are fully mixed and pressed into shape, and then the pressed compact is put into a vacuum sintering furnace and sintered at 1300°C / 1.5 hours to form a titanium alloy sintered compact. Then the sintered green body was forged and deformed at a high temperature of 900°C / 50%, and its mechanical properties were tested.
Embodiment 3
[0023] Weigh Fe: 1.5%, Mo: 2.25%, YH 2 (250 mesh): 1.5%, the balance is hydrogenated dehydrogenated titanium powder, the above powders are fully mixed and pressed into shape, and then the compact is put into a vacuum sintering furnace and sintered at 1300°C / 1.5 hours to form a titanium alloy sintered compact. Then the sintered body was forged and deformed at a high temperature of 1000°C / 50%, and its mechanical properties were tested.
PUM
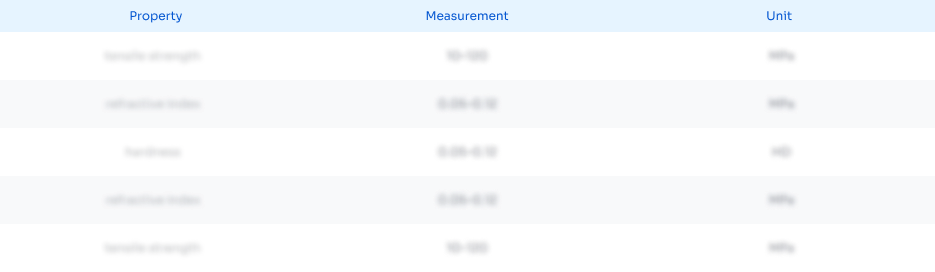
Abstract
Description
Claims
Application Information

- R&D
- Intellectual Property
- Life Sciences
- Materials
- Tech Scout
- Unparalleled Data Quality
- Higher Quality Content
- 60% Fewer Hallucinations
Browse by: Latest US Patents, China's latest patents, Technical Efficacy Thesaurus, Application Domain, Technology Topic, Popular Technical Reports.
© 2025 PatSnap. All rights reserved.Legal|Privacy policy|Modern Slavery Act Transparency Statement|Sitemap|About US| Contact US: help@patsnap.com