ABS color master batch
A color masterbatch and toner technology, applied in the field of plastic coloring, can solve problems such as poor color stability, and achieve the effects of overcoming color instability, small color difference, and reducing production costs
- Summary
- Abstract
- Description
- Claims
- Application Information
AI Technical Summary
Problems solved by technology
Method used
Image
Examples
Embodiment 1
[0017] Under normal temperature and pressure, mix the following components and weight percentages: AS 25%, POE 10%, titanium dioxide 40%, antioxidant 15202%, activated molecular sieve 23%, and mix at high speed for 10 minutes in a high-speed mixer. The screw extruder is melted and blended, the temperature is controlled at 200 ℃, the screw speed is 200r / min, the pigment is uniformly dispersed in the carrier resin through the shearing and mixing of the screw, and then the drawing and pelletizing (the appearance of the masterbatch) It is cylindrical), dried, and packaged to prepare the masterbatch A1 of the present invention.
Embodiment 2
[0019] Under normal temperature and pressure, 70% AS and 30% EMA are mixed in a high-speed mixer for 5 minutes, and a twin-screw extruder is used for melt blending. The temperature is controlled at 220°C and the screw speed is 200r / min. The shearing and mixing of the screw make the two materials uniformly mixed, and then granulation and drying are performed to obtain the desired color masterbatch carrier of the present invention.
[0020] Under normal temperature and pressure, the following components and weight percentages: carrier 35%, titanium dioxide 30%, maleic anhydride grafted polyethylene wax 10%, phosphite 1681%, antioxidant DLTP 5%, surface coating oxidation Calcium 14%, barium sulfate 5%, high-speed mixing in a high-speed mixer for 15 minutes, using a twin-screw extruder for melt blending, the temperature is controlled at 200 ℃, the screw speed is 100r / min, through the shear, Kneading makes the pigments uniformly dispersed in the carrier resin, and then is stretched an...
Embodiment 3
[0022] Under normal temperature and pressure, the following components and weight percentages: carrier AS 25%, EAA 32%, titanium dioxide 15%, lithopone 5%, azo pigment 0.5%, oxidized polyethylene wax 1%, maleic anhydride Branch polypropylene wax 1.5%, antioxidant 17261%, phosphite 6260.5%, stearate 2%, white mineral oil 2%, activated molecular sieve 4%, activated hydrotalcite 3%, barium sulfate 7.5%, at high speed In the mixer, the internal mixing is used for mixing, and then the screw extruder is used for stranding and pelletizing (the masterbatch is cylindrical in appearance) to obtain the masterbatch of the present invention.
PUM
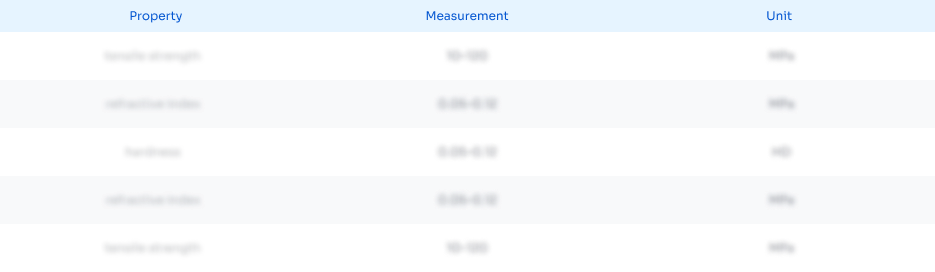
Abstract
Description
Claims
Application Information

- R&D
- Intellectual Property
- Life Sciences
- Materials
- Tech Scout
- Unparalleled Data Quality
- Higher Quality Content
- 60% Fewer Hallucinations
Browse by: Latest US Patents, China's latest patents, Technical Efficacy Thesaurus, Application Domain, Technology Topic, Popular Technical Reports.
© 2025 PatSnap. All rights reserved.Legal|Privacy policy|Modern Slavery Act Transparency Statement|Sitemap|About US| Contact US: help@patsnap.com