Method for producing series magnesia chemical products by using material containing magnesium
A technology for chemical products and materials, applied in the field of comprehensive utilization of magnesium-containing resources, can solve the problems of negative product generation, large amount of sulfuric acid, and low leaching rate, and achieve good product quality, reduced equipment investment, and significant economic benefits
- Summary
- Abstract
- Description
- Claims
- Application Information
AI Technical Summary
Problems solved by technology
Method used
Image
Examples
Embodiment 1
[0037] The raw material is boron mud produced in Liaoning, the composition is (mass fraction): MgO 41%, CO 2 30%, SiO 2 19%, B 2 o 3 2%, Fe 2 o 3 4.0%, CaO 1.8%, Al 2 o 3 2.2%.
[0038] Take an appropriate amount of boron mud and heat it to 900°C for calcination for 5 hours. The product is cooled, ground and mixed evenly with ammonium sulfate. The molar ratio of magnesium oxide to ammonium sulfate is 1:0.7. Raise the temperature of the mixed material to 450° C. and keep it warm for 7 hours to carry out the roasting reaction. The gas released during the reaction process is absorbed by water and used as a raw material for preparing magnesium hydroxide by precipitating magnesium sulfate solution. The product was cooled, dissolved in deionized water, and then subjected to solid-liquid separation under reduced pressure. The filtrate is magnesium sulfate solution, and the filter residue is silicon dioxide, boron oxide, calcium oxide, iron oxide, aluminum oxide and a smal...
Embodiment 2
[0045] The raw material is boron mud produced in Liaoning, the composition is (mass fraction): MgO42%, CO 2 31%, SiO 2 18%, B 2 o 3 2%, Fe 2 o 3 3.5%, CaO 1.5%, Al 2 o 3 2%.
[0046] Take an appropriate amount of boron mud and heat it to 900°C for calcination for 5 hours. The product is cooled, ground and mixed evenly with ammonium sulfate, the molar ratio of magnesium oxide to ammonium sulfate is 1:0.9. Raise the temperature of the mixed material to 500°C and keep it warm for 5 hours, and carry out the roasting reaction. The gas released during the reaction process is pressurized and liquefied, and used as a raw material for preparing magnesium hydroxide by precipitating magnesium sulfate solution. The product was cooled, dissolved in deionized water, and then subjected to solid-liquid separation under reduced pressure. The filtrate is magnesium sulfate solution, and the filter residue is silicon dioxide, boron oxide, calcium oxide, iron oxide, aluminum oxide and...
Embodiment 3
[0053] The raw material is magnesite produced in Liaoning, the composition is (mass fraction) MgO 47.6%, CO 2 45.8%, SiO 2 5.2%, CaO 0.889%, Fe 2 o 3 0.511%.
[0054] Crush the magnesite, heat it to 1100°C and calcinate for 6 hours, cool the product, grind it finely and mix it evenly with ammonium sulfate, the molar ratio of magnesium oxide to ammonium sulfate is 1:0.7. Raise the temperature of the mixed material to 450° C. and keep it warm for 7 hours to carry out the roasting reaction. The gas released during the reaction process is absorbed by water and used as a raw material for preparing magnesium hydroxide by precipitating magnesium sulfate solution. The product is cooled, dissolved in deionized water, and then subjected to solid-liquid separation under reduced pressure. The filtrate is magnesium sulfate solution, and the filter residue is silicon dioxide, calcium oxide, iron oxide, aluminum oxide and a small amount of unreacted magnesium oxide. Recover silica. P...
PUM
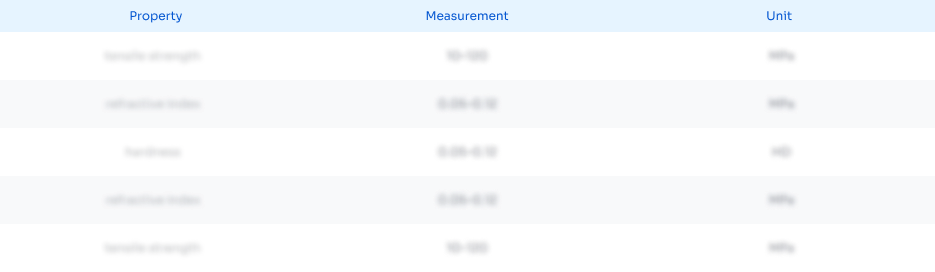
Abstract
Description
Claims
Application Information

- Generate Ideas
- Intellectual Property
- Life Sciences
- Materials
- Tech Scout
- Unparalleled Data Quality
- Higher Quality Content
- 60% Fewer Hallucinations
Browse by: Latest US Patents, China's latest patents, Technical Efficacy Thesaurus, Application Domain, Technology Topic, Popular Technical Reports.
© 2025 PatSnap. All rights reserved.Legal|Privacy policy|Modern Slavery Act Transparency Statement|Sitemap|About US| Contact US: help@patsnap.com