New process for purifying and manufacturing microcrystalline graphite product
A technology of microcrystalline graphite and a new process, which is applied in the field of purification and purification of microcrystalline graphite products, can solve problems such as complex process, high power consumption, and large safety hazards, and achieve good purification effect
- Summary
- Abstract
- Description
- Claims
- Application Information
AI Technical Summary
Problems solved by technology
Method used
Image
Examples
Embodiment Construction
[0050] The present invention is described in detail below in conjunction with accompanying drawing:
[0051] The new process for purification and purification of microcrystalline graphite products described in the present invention includes flotation and alkali-melting acid leaching purification processes.
[0052] (1) The described flotation process is, 1) the graphite raw ore is finely ground to reach a suitable fineness, generally reaching a grinding fineness of -200 mesh with a pass rate of 91.25%, 2) in the finely ground graphite raw ore Add regulator, such as quicklime used in the present invention, and add water, make the pH of the graphite slurry containing quicklime>9, preferably pH=11~12, stir under normal temperature and pressure, the stirring time can be three minutes, 3) add Inhibitor, the inhibitor can be water glass, the preferred modulus is 2.2, the preferred dosage is 2000g / t, stirred at normal temperature and pressure, the stirring time can be three minutes; ...
PUM
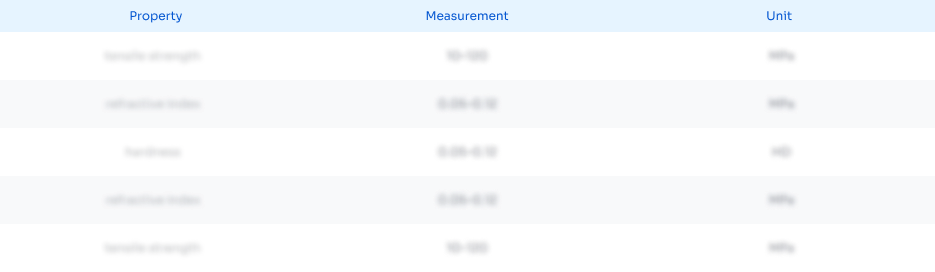
Abstract
Description
Claims
Application Information

- Generate Ideas
- Intellectual Property
- Life Sciences
- Materials
- Tech Scout
- Unparalleled Data Quality
- Higher Quality Content
- 60% Fewer Hallucinations
Browse by: Latest US Patents, China's latest patents, Technical Efficacy Thesaurus, Application Domain, Technology Topic, Popular Technical Reports.
© 2025 PatSnap. All rights reserved.Legal|Privacy policy|Modern Slavery Act Transparency Statement|Sitemap|About US| Contact US: help@patsnap.com