Ultra-fine denier nylon stable fiber production method
A production method and ultra-fine denier technology are applied in the field of synthetic fibers to achieve the effects of cost reduction, expansion of application scope and simple process
- Summary
- Abstract
- Description
- Claims
- Application Information
AI Technical Summary
Problems solved by technology
Method used
Image
Examples
Embodiment 1
[0063] See figure 1 , this example follows the steps below.
[0064] 1) Spinning, on the twin-screw melt spinning equipment, add masterbatch and nylon 6 chips to mix, extrude the melted mixture into the spinneret assembly through the screw, and extrude through the spinneret holes after filtering through sea sand, Form tow; the amount of masterbatch added is 5% of the total weight of the two raw materials;
[0065] The raw material used in this example is nylon 6 chips, the relative viscosity is 2.47±0.02, and the density is 1.14g / cm 3 , and the melting point is 215~222°C. The special masterbatch is based on nylon 6 slices, adding 0.5% antioxidant - antioxidant 168 and antioxidant 1010 (the weight ratio of the two is 1:1), and 0.5% dispersant - poly Ethylene glycol, 0.5% stabilizer--liquid paraffin, 4% modifier--K 2 SO 4 and SrCl 2 (The weight ratio of the two is 1:3) Melt extrusion and granulation on a twin-screw extruder, the melt flow index of the obtained masterbatch ...
PUM
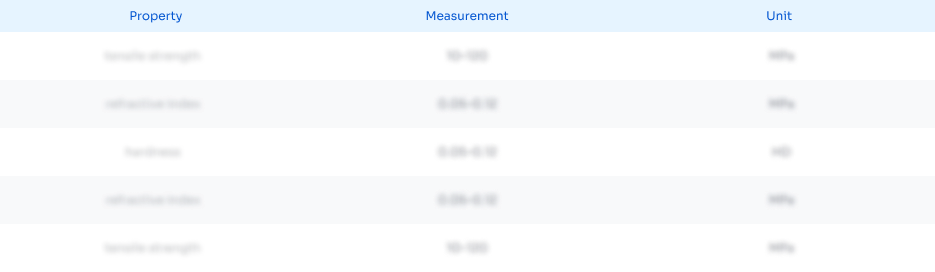
Abstract
Description
Claims
Application Information

- Generate Ideas
- Intellectual Property
- Life Sciences
- Materials
- Tech Scout
- Unparalleled Data Quality
- Higher Quality Content
- 60% Fewer Hallucinations
Browse by: Latest US Patents, China's latest patents, Technical Efficacy Thesaurus, Application Domain, Technology Topic, Popular Technical Reports.
© 2025 PatSnap. All rights reserved.Legal|Privacy policy|Modern Slavery Act Transparency Statement|Sitemap|About US| Contact US: help@patsnap.com