Method for printing printed circuit board double sided characters
A technology for printed circuit boards and printing methods, applied in the directions of printing, printing devices, etc., can solve the problems of easy scratching of printed circuit boards, cumbersome operation of workers, high labor intensity, etc., so as to improve labor production efficiency and reduce labor intensity. , the effect of reducing energy consumption
- Summary
- Abstract
- Description
- Claims
- Application Information
AI Technical Summary
Problems solved by technology
Method used
Examples
Embodiment 1
[0013] (1) The screen plate is fixed to the rear end of the screen printing machine table and can be moved. Put the printed circuit board with a thickness of 1.2mm to be printed on the screen printing machine table and use positioning nails to position it, then put the screen down and print. After the circuit board is aligned, put the adjusted ink on the screen, the squeegee is at a 70 degree angle to the screen, and the squeegee pressure is 6kg / cm 2 Perform printing, open the screen after printing, and take out the printed circuit board on which one side of the text has been printed;
[0014] (2) There are 4 rectangular copper clad laminates on the other screen printing machine, and they are positioned. The 4 copper clad laminates are enclosed in a box. The size of the box is consistent with the process side of the printed circuit board to be printed. The thickness of the copper plate is 1.5mm, the width is 3cm, and the length is slightly shorter than the printed circuit board to...
Embodiment 2
[0017] (1) The screen plate is clamped on the rear end of the screen printing machine table and can be moved. Put the printed circuit board with a thickness of 1.6mm to be printed on the screen printing machine table and use the positioning nails to position it. Put down the screen and the text to be printed. After the printed circuit board is aligned, put the adjusted ink on the screen, the squeegee is at an angle of 80 degrees with the screen, and the squeegee pressure is 7.5kg / cm 2 Perform printing, open the screen after printing, and take out the printed circuit board on which one side of the text has been printed;
[0018] (2) There are 4 rectangular copper clad laminates on the other screen printing machine, and they are positioned. The 4 copper clad laminates are enclosed in a box, and the size of the box is consistent with the process side of the printed circuit board to be printed. The thickness of the copper plate is 1.8mm, the width is 5cm, and the length is slightly sh...
Embodiment 3
[0021] (1) The screen is fixed and clamped on the rear end of the screen printing machine table and can be moved. Put the 2.5mm thickness of the printed circuit board on the screen printing machine table with positioning nails for positioning, and put the screen down and the printing After the printed circuit board is aligned, put the adjusted ink on the screen, the squeegee is at a 75 degree angle to the screen, and the squeegee pressure is 6.8kg / cm 2 Perform printing, open the screen after printing, and take out the printed circuit board printed on one side;
[0022] (2) The other screen printing machine has 4 copper clad laminates on the table and positioned them. The 4 copper clad laminates are enclosed in a box. The size of the box is consistent with the process edge of the printed circuit board to be printed. The thickness of the copper clad laminate 1.6mm, width 4cm, length is slightly shorter than the printed circuit board to be printed. Four positioning nails are install...
PUM
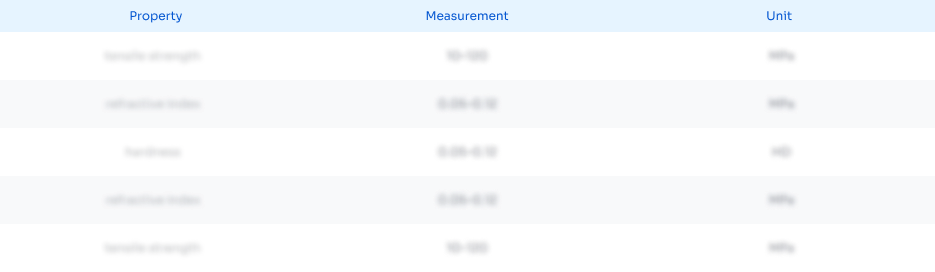
Abstract
Description
Claims
Application Information

- Generate Ideas
- Intellectual Property
- Life Sciences
- Materials
- Tech Scout
- Unparalleled Data Quality
- Higher Quality Content
- 60% Fewer Hallucinations
Browse by: Latest US Patents, China's latest patents, Technical Efficacy Thesaurus, Application Domain, Technology Topic, Popular Technical Reports.
© 2025 PatSnap. All rights reserved.Legal|Privacy policy|Modern Slavery Act Transparency Statement|Sitemap|About US| Contact US: help@patsnap.com