Aluminum preliminary alloy refiner containing titanium and vanadium, aluminum alloy containing titanium and vanadium and preparation method
An aluminum master alloy and refiner technology, which is applied in the field of aluminum and aluminum alloys, can solve the problems of unfavorable aluminum foil processing, large size, poor wettability between liquid aluminum and carbon, etc.
- Summary
- Abstract
- Description
- Claims
- Application Information
AI Technical Summary
Problems solved by technology
Method used
Image
Examples
Embodiment 1
[0083] The raw materials used in this embodiment and the processing steps are as follows:
[0084] The raw material is aluminum powder 1g, (V 0.95 Ti 0.05 ) C powder 99g. The measured aluminum powder and (V 0.95 Ti 0.05 ) C powder is subjected to rolling ball milling, the mass ratio of ball to material is 6:1, the ball milling time is limited to the uniform mixing of raw materials (about 10 hours), and then the uniformly mixed raw materials are pressed into shape, and the compact size is Φ1.6cm×2.5cm, Then put the compact into the heating furnace, and feed in argon or hydrogen at a flow rate of 1.5L / min. After feeding in argon or hydrogen to remove the air in the furnace (about 3 minutes), heat it to 300°C and keep it at 300°C After 4 hours, after the heat preservation is completed, the furnace is cooled to below 100°C and taken out of the furnace, and the vanadium-containing titanium-aluminum master alloy refiner 76.30%V-3.78%Ti-18.92%C-1%Al is obtained.
Embodiment 2
[0086] The raw materials used in this embodiment and the processing steps are as follows:
[0087] The raw materials are 1g of aluminum powder, 5.25g of VC powder and 93.75g of TiC powder. The measured aluminum powder, VC powder, and TiC powder are rolled and ball milled, the mass ratio of ball to material is 6:1, the ball milling time is limited to the uniform mixing of raw materials (about 10 hours), and then the uniformly mixed raw materials are pressed into shape, and compacted The size is Φ1.6cm×2.5cm, and then put the green compact into the heating furnace, and pass in argon or hydrogen, the flow rate is 1.5L / min, and heat it after passing in argon or hydrogen to remove the air in the furnace (3min) Heat it to 700°C and keep it at 700°C for 1 hour. After the heat preservation is over, cool it down to below 100°C and take it out of the furnace to get the vanadium-containing titanium-aluminum master alloy refiner 4.25%V-74.97%Ti-19.78%C-1%Al.
Embodiment 3
[0089] The raw materials used in this embodiment and the processing steps are as follows:
[0090] The raw material is aluminum powder 1g, (V 0.05 Ti 0.95 ) N powder 99g. The measured aluminum powder and (V 0.05 Ti 0.95 )N powder is subjected to rolling ball milling, the mass ratio of ball to material is 10:1, the ball milling time is limited to the uniform mixing of raw materials (about 24 hours), and then the uniformly mixed raw materials are pressed into shape, and the compact size is Φ1.6cm×2.5cm, Then put the compact into the heating furnace and feed nitrogen gas at a flow rate of 5L / min. After the nitrogen gas is fed to remove the air in the furnace (about 3 minutes), heat it to 750°C and keep it at 750°C for 0.5h. Cool the furnace to below 100°C and take out the furnace to obtain a vanadium-containing titanium-aluminum master alloy refiner 4.06%V-72.60%Ti-22.34%N-1%Al.
PUM
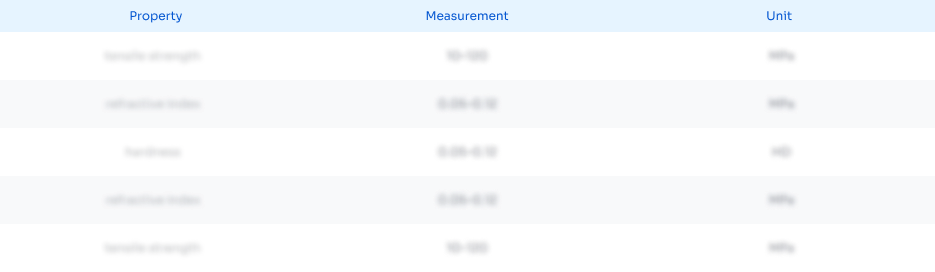
Abstract
Description
Claims
Application Information

- R&D Engineer
- R&D Manager
- IP Professional
- Industry Leading Data Capabilities
- Powerful AI technology
- Patent DNA Extraction
Browse by: Latest US Patents, China's latest patents, Technical Efficacy Thesaurus, Application Domain, Technology Topic, Popular Technical Reports.
© 2024 PatSnap. All rights reserved.Legal|Privacy policy|Modern Slavery Act Transparency Statement|Sitemap|About US| Contact US: help@patsnap.com