Improved regeneration technique for decolorizing and deodorizing waste tyre oil and method for preparing diesel fuel thereof
A waste tire and improved technology, applied in chemical instruments and methods, refined hydrocarbon oil, petroleum industry, etc., can solve the problems of low oil output efficiency, corrosiveness, poor power, etc., and achieve increased contact reaction area and stimulation. The effect of disappearing sexual odor and speeding up reaction time
- Summary
- Abstract
- Description
- Claims
- Application Information
AI Technical Summary
Problems solved by technology
Method used
Examples
specific Embodiment approach 1
[0030] a. Mix the following raw materials according to the weight ratio
[0031] 100 parts of waste tire oil;
[0032] 1 part of catalytic solution;
[0033] 1 core catalyst;
[0034] React for 2 hours after mixing;
[0035] Described catalytic liquid is hydrogen peroxide (H 2 o 2 ), the concentration is 20%;
[0036] The core catalyst is Fe 2 o 3 、Al 2 o 3 a mixture of the two;
[0037] b. Add the anhydrous substance in the upper layer after the mixed reaction in step a to the reactor, then add 1 part by weight of the core catalyst, heat, and collect 94.0 parts by weight of the distillate below the normal pressure of 365 °C;
[0038] c, add 1 weight part concentrated sulfuric acid (concentration 90%) to the distillate in the b step, stir for 20 minutes, add 2 weight parts of white clay to precipitate after 20 minutes, filter with less than 200 mesh filter press or filter sand, get light yellow 91.6 parts by weight of primary diesel oil;
[0039] d. Add 0.05 parts ...
specific Embodiment approach 2
[0040] a. Mix the following raw materials according to the weight ratio
[0041] 100 parts of waste tire oil;
[0042] 8 parts of catalytic solution;
[0043] 5 parts of core catalyst;
[0044] React for 5 hours after mixing;
[0045] Described catalytic liquid is hydrogen peroxide (H 2 o 2 ), concentration 30%;
[0046] The core catalyst is SiO 2 , MnO 2 a mixture of the two;
[0047] b. Add the anhydrous substance in the upper layer after the mixed reaction in step a to the reactor, then add 5 parts by weight of the core catalyst, heat, and collect 94.5 parts by weight of the distillate below 0.09MPA negative pressure at 280°C-300°C;
[0048] c. Add 6 parts by weight of vitriol oil (concentration 95%) to the distillate in the b step, stir for 30 minutes, add 6 parts by weight of white clay to precipitate for 30 minutes, filter with less than 100 mesh filter press or filter sand to obtain light yellow 92.4 parts by weight of primary diesel oil;
[0049] d. Add 0.1 par...
specific Embodiment approach 3
[0050] a. Mix the following raw materials according to the weight ratio
[0051] 100 parts of waste tire oil;
[0052] 5 parts of catalytic solution;
[0053] 3.5 parts of core catalyst;
[0054] React for 3.5 hours after mixing;
[0055] Described catalytic liquid is hydrogen peroxide (H 2 o 2 ), concentration 28%;
[0056] The core catalyst is Fe 2 o 3 , SiO 2 a mixture of the two;
[0057] b. Add the anhydrous substance in the upper layer after the mixed reaction in step a to the reactor, then add 2.6 parts by weight of the core catalyst, heat, and collect 94.7 parts by weight of distillate below 365°C under normal pressure;
[0058] c, add 2 parts by weight of concentrated sulfuric acid (concentration 97%) to the distillate in step b, stir for 25 minutes, add 4 parts by weight of white clay to precipitate for 25 minutes, filter with less than 100 mesh filter press or filter sand to get light yellow 92.8 parts by weight of primary diesel oil;
[0059] d. Add 0.08...
PUM
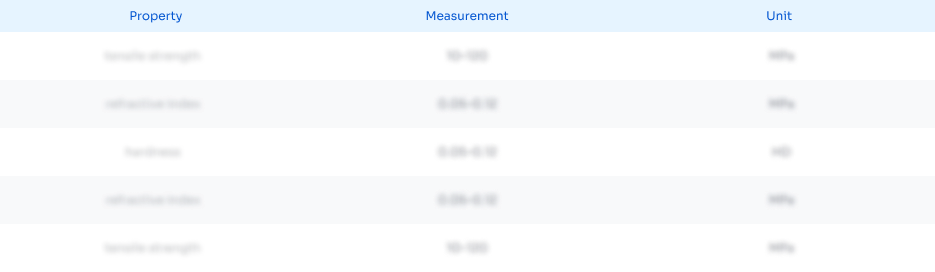
Abstract
Description
Claims
Application Information

- R&D
- Intellectual Property
- Life Sciences
- Materials
- Tech Scout
- Unparalleled Data Quality
- Higher Quality Content
- 60% Fewer Hallucinations
Browse by: Latest US Patents, China's latest patents, Technical Efficacy Thesaurus, Application Domain, Technology Topic, Popular Technical Reports.
© 2025 PatSnap. All rights reserved.Legal|Privacy policy|Modern Slavery Act Transparency Statement|Sitemap|About US| Contact US: help@patsnap.com