Conversion of a multihydroxylated-aliphatic hydrocarbon or ester thereof to a chlorohydrin
A technology of polyhydroxylation and aliphatic hydrocarbons, applied in the preparation of organic compounds, catalysts for physical/chemical processes, catalysts for organic compounds/hydrides/coordination complexes, etc., can solve the problem of inconsistent by-products and hindered reaction rates in economic production , low conversion rate and other issues, to achieve the effect of improved conversion rate, large conversion rate, and method simplification
- Summary
- Abstract
- Description
- Claims
- Application Information
AI Technical Summary
Problems solved by technology
Method used
Image
Examples
Embodiment 1
[0114] Example 1 - Preparation of chlorohydrins from glycerol
[0115] to a 100 mL Hastelloy C equipped with a magnetically driven stirrer, internal cooling coil, and thermocouple TM Glycerin (30.0 g, purchased from Sigma-Aldrich Chemical Corporation) and glacial acetic acid (4.5 g, purchased from JT Baker Corporation) were added to the Parr reactor. The reactor was sealed, pressurized to 90 psig with anhydrous hydrogen chloride gas (Airgas Corporation), and heated to 93° C. for 90 minutes and maintained at 90 psig with anhydrous hydrogen chloride gas, after which the reactor was cooled and brought to room temperature (about 25° C. ) to exhaust. The reactor contents (65.9 g) were collected, analyzed by gas chromatography (GC) and found to contain the following products: 1,3-dichloropropan-2-ol and its acetate (92.6 mol% total) and 2,3 - Dichloropropan-1-ol and its acetate (total 1.7 mol%). In addition, many monochlorinated compounds (4.4 mol% in total) and unreacted glycer...
Embodiment 2
[0116] Example 2 - Preparation of Chlorohydrins from Glycerol / Glyceride Mixtures
[0117] To 200mL Hastelloy C TM A 10 mL glass measuring flask containing dry glycerol (Aldrich, pre-dried through molecular sieves, 91 mg, 0.99 mmol) and glycerol triacetate (Aldrich, triacetate of glycerol, 457 mg, 2.10 mmole) was added to the autoclave . The reactor was sealed and pressurized to 40 psig with nitrogen (three pressure cycles) and brought to 110°C with stirring after nitrogen venting. Anhydrous HCl was introduced under a constant pressure of 76 psig and the reaction was allowed to proceed for 3 hours. The reactor was vented to provide a product which was found to comprise 25.90 area % 1,3-dichloropropan-2-ol, 68.34 area % 1,3-dichloro-2-acetoxypropane, 1.57 area % 1,2-dichloro-3-acetoxypropane, 2.86 area % of 2-chloropropane-1,3-diacetoxypropane and no detectable glycerol, triacetin or 1,2 , 3-trichloropropane, as determined analytically by GC flame ionization detection.
Embodiment 3
[0118] Example 3 - Preparation of chlorohydrins from crude glycerin
[0119] To a 100 mL Hastelloy equipped with a magnetically driven stirrer, internal cooling coil, and thermocouple TM Crude glycerin (30.0 g, purchased from Interwest Corporation) and glacial acetic acid (0.6 g, purchased from JT Baker Corporation) were added to the C Parr reactor. The reactor was sealed, pressurized to 120 psig with anhydrous hydrogen chloride gas (Airgas Corporation), and heated to 120° C. for 90 minutes while maintaining the pressure at 120 psig with anhydrous hydrogen chloride gas. After this time, the reactor was cooled and vented at room temperature. The reactor contents (57.2 g) were collected as a moving liquid containing suspended white solids.
[0120] The above procedure was repeated and 58.0 g of reactor contents were collected from the second reaction. The two reaction products (57.2 g and 58.0 g) were then combined.
[0121] After filtration to remove white solids, sodium a...
PUM
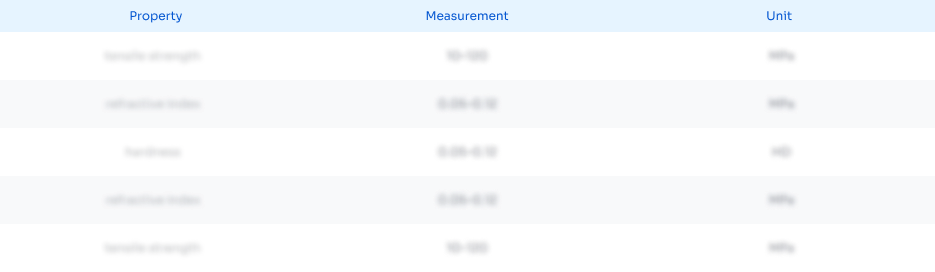
Abstract
Description
Claims
Application Information

- Generate Ideas
- Intellectual Property
- Life Sciences
- Materials
- Tech Scout
- Unparalleled Data Quality
- Higher Quality Content
- 60% Fewer Hallucinations
Browse by: Latest US Patents, China's latest patents, Technical Efficacy Thesaurus, Application Domain, Technology Topic, Popular Technical Reports.
© 2025 PatSnap. All rights reserved.Legal|Privacy policy|Modern Slavery Act Transparency Statement|Sitemap|About US| Contact US: help@patsnap.com