Powder cleaning-free gluing production method of laminated glass
A technology of laminated glass and production method, which is applied in the field of laminated glass gluing production without cleaning the silicon powder layer, which can solve the problems of dust in the working environment, high scrap rate, energy waste, etc., so as to reduce the probability of optical distortion and eliminate The existence of water stains, the effect of reducing the number of handling
- Summary
- Abstract
- Description
- Claims
- Application Information
AI Technical Summary
Problems solved by technology
Method used
Image
Examples
Embodiment Construction
[0027] In a specific embodiment of the production method of laminated glass without clear powder gluing of the present invention, its technological process is as follows figure 2 As shown, first inspect the glass raw material A10, then perform operations such as cutting A20, edging A30, cleaning / drying A40, and inspect whether the glass is qualified; then use the prepared screen to screen / dry the glass A50, etc.; then Silicon powder and water are prepared into a silicon powder solution, and filtered; then use the prepared silicon powder solution to spray a layer of uniform thin silicon powder layer on the air surface of the glass outer sheet, and dry it, so that the glass surface adheres to the Thin silicon powder layer, and match the outer glass with the inner glass A60; then use the hot bending mold to bend the glass A70; finally lay the film laminated A80 directly between the hot bent glass, and then pass Preheating / prepressing furnace (IKU) for cold pumping (vacuum) and h...
PUM
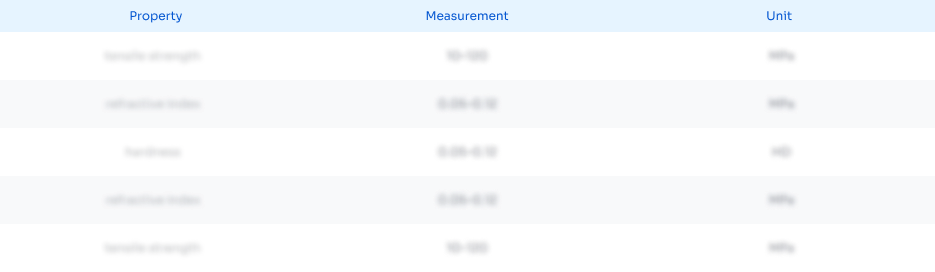
Abstract
Description
Claims
Application Information

- Generate Ideas
- Intellectual Property
- Life Sciences
- Materials
- Tech Scout
- Unparalleled Data Quality
- Higher Quality Content
- 60% Fewer Hallucinations
Browse by: Latest US Patents, China's latest patents, Technical Efficacy Thesaurus, Application Domain, Technology Topic, Popular Technical Reports.
© 2025 PatSnap. All rights reserved.Legal|Privacy policy|Modern Slavery Act Transparency Statement|Sitemap|About US| Contact US: help@patsnap.com