Method for preparing aluminum and coproducing cement from flyash
A technology of alumina and fly ash, which is applied in the production of alumina/aluminum hydroxide and cement, can solve the problems of high cost, high energy consumption, and high sintering temperature, and achieve the effect of facilitating industrialization and low energy consumption
- Summary
- Abstract
- Description
- Claims
- Application Information
AI Technical Summary
Problems solved by technology
Method used
Image
Examples
Embodiment 1
[0023] The composition of raw fly ash is: Al 2 o 3 : 40%, SiO 2 : 48%, Fe 2 o 3 : 3%, CaO: 3%, TiO 2 :1%. The composition of the raw coal fly ash can also adopt other components and specific dosages, any conventional fly ash can be used, which cannot be used to limit the protection scope of the present invention.
[0024] Limestone is calcined at 1200°C to obtain active lime; fly ash, lime, Na 2 CO 3 Mixed ingredients with a small amount of coal powder, in which CaO and SiO 2 The molar ratio is 2:1, Na 2 O and Al 2 o 3 The molar ratio is 1:1 to prepare raw slurry; sinter the raw slurry at 1200°C to obtain clinker containing sodium aluminate, sodium ferrite and dicalcium silicate; Grind and dissolve to obtain crude liquid and residue, and the resulting calcium-silicon slag is used to prepare cement after washing; the crude sodium aluminate solution is desiliconized under pressure at 165°C, and then added lime milk for deep desiliconization to obtain sodium aluminate ...
Embodiment 2
[0026] The fly ash composition is the same as in Example 1.
[0027] Limestone is calcined at 1200°C to obtain active lime. fly ash, lime, Na 2 CO 3 Mixed ingredients with a small amount of coal powder, in which CaO and SiO 2 The molar ratio is 1.8:1, Na 2 O and Al 2 o 3 The molar ratio was 0.8:1 to prepare raw slurry. The raw material slurry is sintered at 1100°C to obtain clinker containing sodium aluminate, sodium ferrite and dicalcium silicate; the clinker is broken at 70°C and eluted by a second-stage mill to obtain crude liquid and residue, and the resulting calcium-silicon The slag is used to prepare cement after washing; the CO produced when calcined limestone is passed into the crude liquid 2 , using pressurized carbon in the carbon tank for carbonation and decomposition to obtain high-silicon aluminum hydroxide; 2 O180g / L alkali solution is dissolved under pressure, the residence time is 40min, and pure sodium aluminate solution is obtained after solid-liquid...
Embodiment 3
[0029] The fly ash composition is the same as in Example 1.
[0030] Limestone is calcined at 1200°C to obtain active lime. fly ash, lime, Na 2 CO 3 Mixed ingredients with a small amount of coal powder, in which CaO and SiO 2 The molar ratio is 2.4:1, Na 2 O and Al 2 o 3 The molar ratio is 1.6:1 to prepare raw slurry; sinter the raw slurry at 1400°C to obtain clinker containing sodium aluminate, sodium ferrite and dicalcium silicate; Dissolution to obtain liquid crude liquid and residue, the resulting calcium silicate slag is used to prepare cement after washing; the CO produced when calcined limestone is passed into the crude liquid 2 , using pressurized carbon in the carbon tank for carbonation and decomposition to obtain high-silicon aluminum hydroxide; 2 The alkaline solution of O200g / L is pressurized and dissolved, and the residence time is 60min. After solid-liquid separation, pure sodium aluminate solution is obtained; in the seed sub-trough, aluminum hydroxide c...
PUM
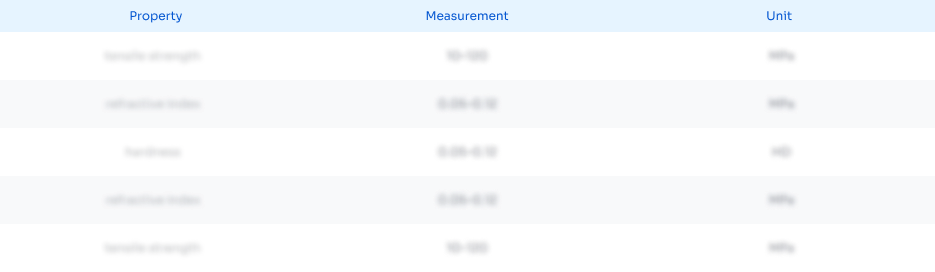
Abstract
Description
Claims
Application Information

- R&D
- Intellectual Property
- Life Sciences
- Materials
- Tech Scout
- Unparalleled Data Quality
- Higher Quality Content
- 60% Fewer Hallucinations
Browse by: Latest US Patents, China's latest patents, Technical Efficacy Thesaurus, Application Domain, Technology Topic, Popular Technical Reports.
© 2025 PatSnap. All rights reserved.Legal|Privacy policy|Modern Slavery Act Transparency Statement|Sitemap|About US| Contact US: help@patsnap.com