Method for preparing water-resistant high-strength functional paper
A high-strength, water-resistant technology, applied in the field of pulp and paper, can solve the problems of lack of dimensional stability and loss of sealing of paper sheets, and achieve the effect of overcoming the increase of paper brittleness and enhancing toughness and strength
- Summary
- Abstract
- Description
- Claims
- Application Information
AI Technical Summary
Problems solved by technology
Method used
Examples
Embodiment 1
[0012] Example 1: First, add anhydrous CaCl in tetrahydrofuran (THF) 2 , after dehydration for 24 hours, filtered to obtain anhydrous tetrahydrofuran (THF); secondly, polyethylene glycol (PEG400) was added to 3-isocyanate methylene-3,5,5-trimethylcyclohexyl isocyanate (IPDI ) to obtain mixture A, wherein the molar ratio of polyethylene glycol to 3-isocyanate methylene-3,5,5-trimethylcyclohexyl isocyanate (IPDI) is 1:1; Make the mass concentration of mixture A in water tetrahydrofuran (THF) be 12%, then add dibutyltin dilaurate of 0.05% of the mass of anhydrous tetrahydrofuran (THF) as a catalyst, use steam to heat to 60 ° C, and stir to obtain a mixed solution ; Then, soak the paper that has been dried at 105°C for 4 hours in the mixed solution, and control the temperature at 60°C for 5 minutes, then take out the paper and dry it at 120°C for 10 minutes under a vacuum of 1.1Mpa to remove excess organic solvent; finally, heat and cure the paper at 120°C for 5 minutes to obtain...
Embodiment 2
[0013] Example 2: First, add anhydrous CaCl in tetrahydrofuran (THF) 2 , after dehydration for 24 hours, filtered to obtain anhydrous tetrahydrofuran (THF); secondly, polyethylene glycol (PEG400) was added to 3-isocyanate methylene-3,5,5-trimethylcyclohexyl isocyanate (IPDI ) to obtain mixture A, wherein the molar ratio of polyethylene glycol to 3-isocyanate methylene-3,5,5-trimethylcyclohexyl isocyanate (IPDI) is 1:3; Make the mass concentration of mixture A in water tetrahydrofuran (THF) be 14%, then add dibutyltin dilaurate of 0.05% of the mass of anhydrous tetrahydrofuran (THF) as a catalyst, use steam to heat to 62 ° C, stir to obtain a mixed solution ; Then, soak the paper that has been dried at 105°C for 4 hours in the mixed solution, and control the temperature at 62°C for 5 minutes, then take out the paper and dry it at 100°C for 10 minutes under a vacuum of 0.8Mpa to remove excess organic solvent; finally, heat and cure the paper at 130°C for 5 minutes to obtain wat...
Embodiment 3
[0014] Example 3: First, add anhydrous CaCl in tetrahydrofuran (THF) 2 , after dehydration for 24 hours, filtered to obtain anhydrous tetrahydrofuran (THF); secondly, polyethylene glycol (PEG400) was added to 3-isocyanate methylene-3,5,5-trimethylcyclohexyl isocyanate (IPDI ) to obtain mixture A, wherein the molar ratio of polyethylene glycol to 3-isocyanate methylene-3,5,5-trimethylcyclohexyl isocyanate (IPDI) is 1:2; Make the mass concentration of mixture A in water tetrahydrofuran (THF) be 10%, then add dibutyltin dilaurate of 0.05% by mass of anhydrous tetrahydrofuran (THF) as a catalyst, use steam to heat to 61 ° C, and stir to obtain a mixed solution ; Then, soak the paper that has been dried at 105°C for 4 hours in the mixed solution, and control the temperature at 61°C for 5 minutes, then take out the paper and dry it at 115°C for 10 minutes under a vacuum of 1.2Mpa to remove excess organic solvent; finally, heat and cure the paper at 123°C for 5 minutes to obtain wat...
PUM
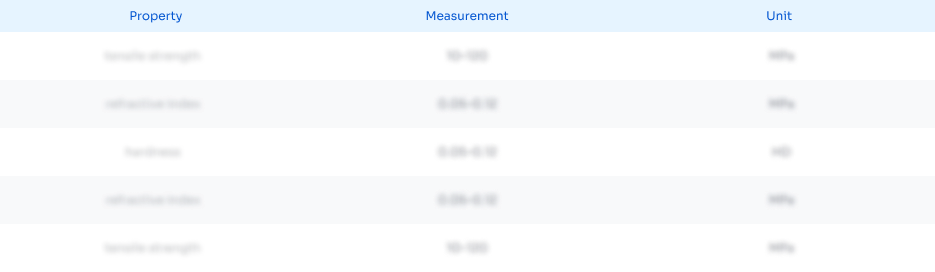
Abstract
Description
Claims
Application Information

- Generate Ideas
- Intellectual Property
- Life Sciences
- Materials
- Tech Scout
- Unparalleled Data Quality
- Higher Quality Content
- 60% Fewer Hallucinations
Browse by: Latest US Patents, China's latest patents, Technical Efficacy Thesaurus, Application Domain, Technology Topic, Popular Technical Reports.
© 2025 PatSnap. All rights reserved.Legal|Privacy policy|Modern Slavery Act Transparency Statement|Sitemap|About US| Contact US: help@patsnap.com