Zinc smelting process by neutralization and hydrolysis iron removal method
A process and zinc smelting technology, which is applied in the field of zinc smelting process by neutralization hydrolysis iron removal method, can solve the problems of short zinc indium production cost, high zinc indium production cost, long process flow, etc., and achieve good impurity removal effect, The effect of reducing energy consumption and shortening the process flow
- Summary
- Abstract
- Description
- Claims
- Application Information
AI Technical Summary
Problems solved by technology
Method used
Image
Examples
Embodiment 1
[0039] A kind of process of zinc smelting by neutralization hydrolysis deironing method (referring to figure 1 ), using the hydrometallurgy process, including the following procedures:
[0040] A, leaching section: the leaching section includes a neutral leaching process, a low-acid leaching process and a high-acid leaching process;
[0041] A1. Neutral leaching process: add the neutralized hydrolysis supernatant and waste electrolyte to the neutral leaching tank to prepare the neutral leaching pre-liquid according to the initial acid requirements of neutral leaching, and add manganese dioxide after heating to 50°C. Add zinc calcine dust for leaching, the natural reaction heat (that is, the heat naturally generated during the reaction) reaches 65-70°C, and the reaction time is 30-60 minutes; the output neutral leaching pulp is sent to the neutral leaching dense tank to settle, The output neutral leaching supernatant is sent to the neutral leaching supernatant storage tank, an...
Embodiment 2
[0054] A kind of process of zinc smelting by neutralization hydrolysis deironing method (referring to figure 1 ), using the hydrometallurgy process, including the following procedures:
[0055] A, leaching workshop section: its specific operation steps and technological conditions are identical with embodiment one;
[0056] B, neutralization and hydrolysis process: its specific operation steps are identical with embodiment one, and difference is:
[0057] The technical conditions of the neutralization and hydrolysis process are as follows: initial reaction acid: 10-20g / L, reaction temperature: 5-40°C, reaction time: 40-65 minutes, final reaction acid: PH=3.6-4.2, solid-liquid ratio 1: Between 6 and 8.
Embodiment 3
[0059] A kind of process of zinc smelting (containing extraction indium) by neutralization hydrolysis deironing method (referring to figure 2 ), using the hydrometallurgy process, including the following procedures:
[0060] A, leaching workshop section: its specific operation steps and technological conditions are identical with embodiment one;
[0061] B. Neutralization and hydrolysis process: its specific operation steps are the same as in Example 1, the difference is that the neutralization and hydrolysis iron slag produced in the dense tank is sent to acid leaching for indium-containing iron slag (i.e. neutralization and hydrolysis bottom flow press filter residue) The process is acid leached;
[0062] The technical conditions of the neutralization hydrolysis process are as follows: initial reaction acid: 15~30g / L, reaction temperature: 10~40°C, reaction time: 45~70 minutes, final reaction acid: PH=3.6~4.3, solid-liquid ratio 1: Between 6 and 8.
[0063] C. Acid leach...
PUM
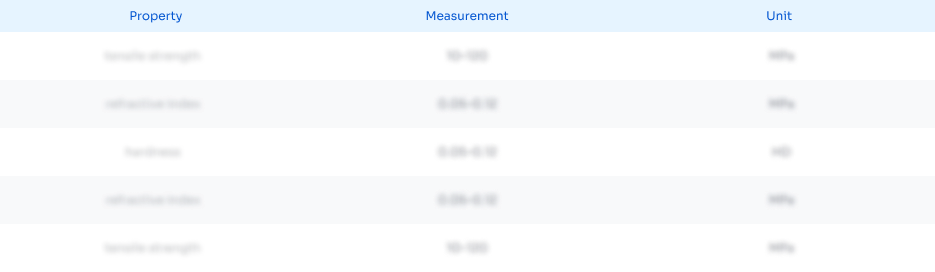
Abstract
Description
Claims
Application Information

- R&D Engineer
- R&D Manager
- IP Professional
- Industry Leading Data Capabilities
- Powerful AI technology
- Patent DNA Extraction
Browse by: Latest US Patents, China's latest patents, Technical Efficacy Thesaurus, Application Domain, Technology Topic, Popular Technical Reports.
© 2024 PatSnap. All rights reserved.Legal|Privacy policy|Modern Slavery Act Transparency Statement|Sitemap|About US| Contact US: help@patsnap.com