Hydro-conversion combination method for coal tar fraction with different boiling ranges
A combined method and hydroconversion technology, which is applied in the fields of hydroprocessing process, petroleum industry, and hydrocarbon oil treatment, can solve the problems of inability to select performance catalysts and operating conditions, unstable properties of mixed coal tar, and excessive pressure drop of catalyst bed. Major and other issues
- Summary
- Abstract
- Description
- Claims
- Application Information
AI Technical Summary
Problems solved by technology
Method used
Examples
Embodiment 1
[0147] The properties of medium-temperature coal tar are shown in Table 1. After the temperature is raised to 80°C, the first-stage filtration is completed, and after the temperature is further raised to 170°C, the second-stage filtration and the first-stage vacuum flash dehydration are completed. After the first-stage dehydration, the medium-temperature coal tar is further heated under negative pressure conditions. Finally, complete vacuum distillation separation (complete secondary dehydration at the same time), set fractionation tower feed heating furnace, fractionation tower top pressure is ~ 0.03MPa (absolute pressure), fractionation tower lower section is steam stripping section, fractionation tower upper section It is the rectification section, and all the coal tar is separated into the top oil (conventional boiling point lower than 250°C) discharged from the top reflux tank, the oil extracted from the middle section of the tower (conventional boiling point 250-330°C) and...
Embodiment 2
[0162] Compared with Example 1, in this example, the third hydrogenation reaction effluent is introduced into the second high-pressure separation part to be separated and recovered jointly with the second hydrogenation reaction effluent, so as to simplify the separation and recovery process of the second hydrogenation reaction effluent. The entire second hydrotreated heavy oil cycle constitutes the entire cycle cracking process.
Embodiment 3
[0164]Compared with Example 1, in this example, the inlet of the catalyst bed after the third hydrogenation reaction effluent is introduced into the demetallization catalyst bed of the second hydrogenation reaction part is in contact with the catalyst bed. All the second hydrotreated heavy oil cycles constitute the entire cycle cracking process. Utilize the second hydrogenation reaction part to carry out hydrogenation refining on the third hydrogenation reaction effluent, and use the third hydrogenation reaction effluent to increase the heat capacity of the second hydrogenation reaction part, reduce the temperature rise of the second hydrogenation reaction part, and stabilize operate. The third hydrogenation reaction part does not use post-refining catalyst.
PUM
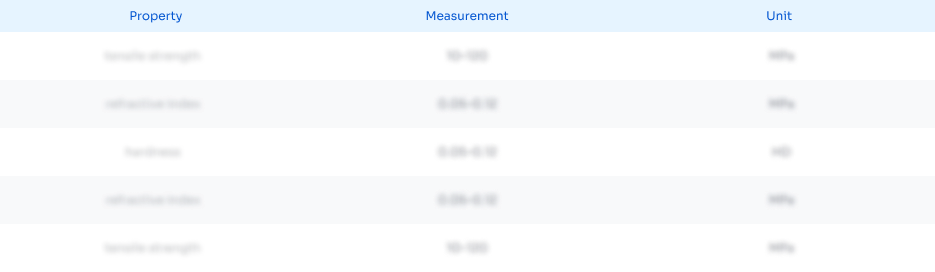
Abstract
Description
Claims
Application Information

- R&D
- Intellectual Property
- Life Sciences
- Materials
- Tech Scout
- Unparalleled Data Quality
- Higher Quality Content
- 60% Fewer Hallucinations
Browse by: Latest US Patents, China's latest patents, Technical Efficacy Thesaurus, Application Domain, Technology Topic, Popular Technical Reports.
© 2025 PatSnap. All rights reserved.Legal|Privacy policy|Modern Slavery Act Transparency Statement|Sitemap|About US| Contact US: help@patsnap.com