Novel method for synthesizing quaternary ammonium salts
A quaternary ammonium salt and a new method technology, which is applied in the field of preparation of quaternary ammonium salt, can solve the problems that the industrialization process of quaternary ammonium salt has not yet been found, high production cost, and large consumption
- Summary
- Abstract
- Description
- Claims
- Application Information
AI Technical Summary
Problems solved by technology
Method used
Examples
Embodiment 1
[0012] Weigh 400 kg of dodecyl dimethyl tertiary amine and place it in a 1000 liter enamel reaction kettle, pump 204 kg of concentrated hydrochloric acid, 125 kg of methanol and 0.4 kg of ionic liquid 1-ethyl-3 at a flow rate of 150 kg / hour - Methylimidazole hydrochloride, stirred at 55° C. and reacted under a nitrogen atmosphere under normal pressure, and the reaction time was 3 hours. After the reaction product was vacuum-dried (the drying temperature was controlled at 80°C), it was added to a 1000L high-pressure reactor, and after the reactor was purged three times with nitrogen, 188 kg of dimethyl carbonate and 80 kg of The methanol mixture was closed and reacted at a reaction temperature of 175° C. and a reaction pressure of 1.7 MPa, and reacted for 12 hours under stirring. The reaction product was vacuum-dried (the drying temperature was controlled at 80° C.) to obtain 492 kg of dodecyltrimethylammonium chloride, with a yield of 99.4% and a purity of 99.2% through quanti...
Embodiment 2
[0014] Weigh 400 kg of dodecyl dimethyl tertiary amine and place it in a 1000 liter enamel reactor, pump 298 kg of hydrobromic acid, 125 kg of ethanol and 0.4 kg of ionic liquid 1-ethyl- The mixture of 3-methylimidazolium hydrobromide was stirred and reacted at 50° C. for 3 hours, and reacted under normal pressure under a nitrogen atmosphere. After the reaction product was vacuum-dried (the drying temperature was controlled at 80°C), it was added to a 1000L high-pressure reactor, and after the reactor was purged three times with nitrogen, 188 kg of dimethyl carbonate and 80 kg of The methanol mixture was closed and reacted at a reaction temperature of 175° C. and a reaction pressure of 1.7 MPa, and reacted for 12 hours under stirring. The reaction product was vacuum dried (the drying temperature was controlled at 80° C.) to obtain about 573 kg of dodecyltrimethylammonium bromide with a yield of 99.1% and a purity of 99.2%.
Embodiment 3
[0016] Weigh 400 kg of tetradecyl dimethyl tertiary amine and place it in a 1000 liter enamel reaction kettle, pump 180 kg of concentrated hydrochloric acid, 125 kg of acetonitrile and 0.4 kg of ionic liquid 1-butyl-3 at a flow rate of 125 kg / hour - The mixture of methylimidazole hydrochloride was stirred and reacted at 60° C. for 3 hours, and reacted under normal pressure under a nitrogen atmosphere. After the reaction product was vacuum-dried (the drying temperature was controlled at 80°C), it was added to a 1000L high-pressure reactor, and after the reactor was purged three times with nitrogen, 168 kg of dimethyl carbonate and 80 kg of The methanol mixture was closed and reacted at a reaction temperature of 175° C. and a reaction pressure of 1.7 MPa, and reacted for 12 hours under stirring. The reaction product was vacuum-dried (the drying temperature was controlled at 80° C.) to obtain about 482 kg of tetradecyltrimethylammonium chloride with a yield of 99.6% and a purity ...
PUM
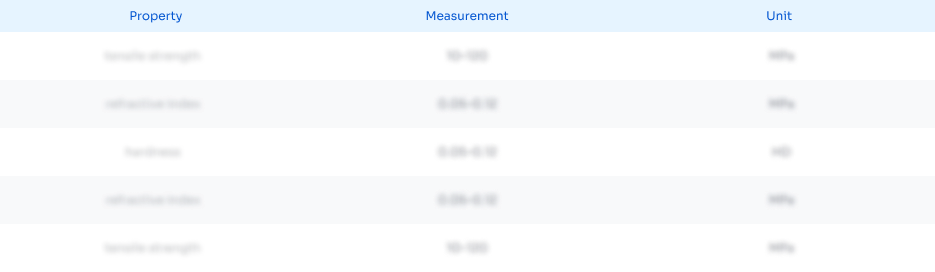
Abstract
Description
Claims
Application Information

- R&D Engineer
- R&D Manager
- IP Professional
- Industry Leading Data Capabilities
- Powerful AI technology
- Patent DNA Extraction
Browse by: Latest US Patents, China's latest patents, Technical Efficacy Thesaurus, Application Domain, Technology Topic, Popular Technical Reports.
© 2024 PatSnap. All rights reserved.Legal|Privacy policy|Modern Slavery Act Transparency Statement|Sitemap|About US| Contact US: help@patsnap.com