Preparation method for Ti3SiC2 ceramic material
A ceramic material and wet process technology, applied in the field of ceramic material manufacturing, can solve the problems of incapable of large-scale industrial production, many impurities, difficult to control the purity, etc., and achieve the effect of low cost, low firing temperature, uniform and dense material structure
- Summary
- Abstract
- Description
- Claims
- Application Information
AI Technical Summary
Problems solved by technology
Method used
Image
Examples
Embodiment 1
[0016] Embodiment 1, at first, the Ti powder of 66.6%, the Si powder of 20.1% and the C powder of 13.3% are made mixture by mass percentage; Next, add the sodium stearate dispersant of mixture quality 0.5% and 2.698 % Aluminum powder is milled by dry method with a QM-ISP2 planetary ball mill with a rotation speed of 400r / min, the mass ratio of the material to the ball is 1:10, and the ball milling time is 18 hours, so that it can be mechanically alloyed to refine the grains, and at the same time in situ The reaction produces a small amount of SiC, Ti 5 Si 3 For the intermediate phase, before ball milling, first pass argon into the ball milling cylinder to discharge the air in the ball milling cylinder; then, use ethanol solution to wet the powder after ball milling, and then vacuum dry at 55°C for 28 hours; the dried The powder is put into a graphite grinding tool and dry-pressed, and then hot-pressed and sintered at 1200°C and 10MPa under vacuum for 1.5 hours to obtain Ti 3...
Embodiment 2
[0017] Embodiment 2, at first, the Ti powder of 68.5%, the Si powder of 19.5% and the C powder of 12% are made mixture by mass percentage; Secondly, add the sodium stearate dispersant of mixture quality 0.5% and 2.698 % Aluminum powder is milled by dry method with a QM-ISP2 planetary ball mill with a rotation speed of 400r / min, the mass ratio of material to ball is 1:10, and the ball milling time is 20 hours, so that it can be mechanically alloyed to refine the grains, and at the same time in situ The reaction produces a small amount of SiC, Ti 5 Si 3 For the intermediate phase, before ball milling, first pass argon gas into the ball mill cylinder to discharge the air in the ball mill cylinder; then, use ethanol solution to wet the powder after ball milling, and then vacuum dry at 50°C for 30 hours; the dried The powder is put into a graphite grinding tool and dry-pressed, and then hot-pressed and sintered at 1300°C and 15MPa under vacuum for 2 hours to obtain Ti 3 SiC 2 Ce...
Embodiment 3
[0018] Embodiment 3, at first, 68.5% Ti powder, 20.1% Si powder and 11.4% C powder are made into mixture by mass percentage; Secondly, add the sodium stearate dispersant of mixture quality 0.5% and 2.698 % Aluminum powder is milled by dry method with a QM-ISP2 planetary ball mill with a rotation speed of 400r / min, the mass ratio of material to ball is 1:10, and the ball milling time is 22 hours, so that it can be mechanically alloyed to refine the grains, and at the same time in situ The reaction produces a small amount of SiC, Ti 5 Si 3 For the intermediate phase, before the ball milling, argon gas was introduced into the ball milling cylinder to discharge the air in the ball milling cylinder; then, the powder after ball milling was taken by ethanol solution wet method, and then vacuum-dried at 60°C for 25 hours; the dried The powder is put into a graphite grinding tool and dry-pressed to form, and then hot-pressed and sintered at 1250 ° C and 20 MPa pressure for 2 hours und...
PUM
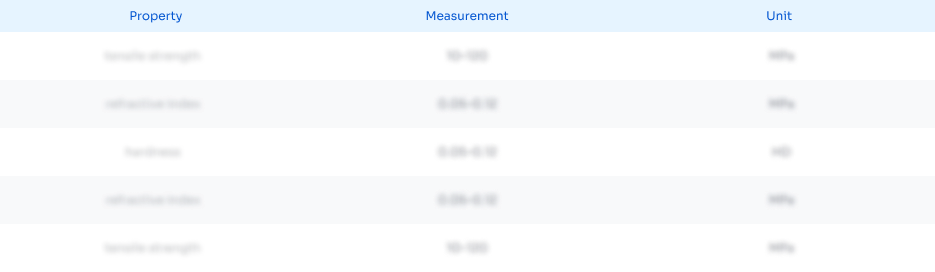
Abstract
Description
Claims
Application Information

- R&D
- Intellectual Property
- Life Sciences
- Materials
- Tech Scout
- Unparalleled Data Quality
- Higher Quality Content
- 60% Fewer Hallucinations
Browse by: Latest US Patents, China's latest patents, Technical Efficacy Thesaurus, Application Domain, Technology Topic, Popular Technical Reports.
© 2025 PatSnap. All rights reserved.Legal|Privacy policy|Modern Slavery Act Transparency Statement|Sitemap|About US| Contact US: help@patsnap.com