Magnesium-based brazing filler metal alloy and preparation method thereof
A brazing filler metal and alloy technology, applied in the field of magnesium alloy brazing filler metal and magnesium-based brazing filler metal alloy, can solve problems such as unstable brazing filler metal quality and performance, influence on brazing filler metal macrostructure, and lower working temperature, so as to improve spreadability, Low cost and improved shear strength
- Summary
- Abstract
- Description
- Claims
- Application Information
AI Technical Summary
Problems solved by technology
Method used
Image
Examples
Embodiment 1
[0023] Embodiment 1: Take 80g pure Al ingot, 5330g pure Mg ingot, 200g pure Sn bar, 0.15g pure Be block, 0.15g pure Te ingot, 260g pure Bi powder, 3927g pure Zn bar, 200g Mg-La intermediate alloy block (Wherein the mass percent composition of La is 15%) put in SF 6 Heat and melt in an electric furnace crucible in a protective atmosphere. When the temperature rises to 680-700°C, keep it warm for 5-10 minutes and then pour it into a steel ingot mold preheated to 200°C to cool to obtain a magnesium-based solder alloy.
Embodiment 2
[0024] Embodiment two: get 50g pure Al ingot, 4873g pure Mg ingot, 50g pure Sn bar, 0.3g pure Be block, 0.3g pure Te ingot, 800g pure Bi powder and 3959g pure Zn ingot, 267g Mg-La alloy block ( Wherein the mass percent content of La is 15%), put in the electric furnace crucible of SF6 protection atmosphere, heat and melt, when temperature rises to 680~700 ℃, pour into the steel ingot that preheats to 200 ℃ after keeping warm for 5~10 minutes After cooling in the mold, a magnesium-based solder alloy is obtained.
Embodiment 3
[0025] Embodiment three: according to 0.5%Al, 51%Mg, 0.5%Sn, 0.001%Be, 0.001%Te, 0.1%La, 2.6%Bi, all the other are Zn weight percent to carry out batching, prepare according to the method of embodiment one, obtain product1.
PUM
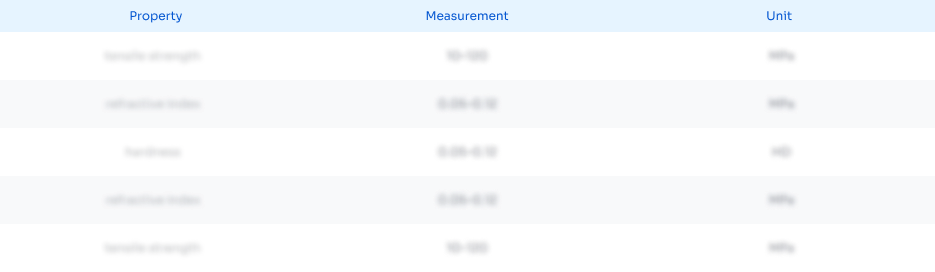
Abstract
Description
Claims
Application Information

- R&D Engineer
- R&D Manager
- IP Professional
- Industry Leading Data Capabilities
- Powerful AI technology
- Patent DNA Extraction
Browse by: Latest US Patents, China's latest patents, Technical Efficacy Thesaurus, Application Domain, Technology Topic, Popular Technical Reports.
© 2024 PatSnap. All rights reserved.Legal|Privacy policy|Modern Slavery Act Transparency Statement|Sitemap|About US| Contact US: help@patsnap.com