Purifying method for boiler fume
A boiler flue gas and boiler technology, which is applied in the field of reducing harmful substances in boiler flue gas, can solve the problems of high investment costs and high equipment operating costs, and achieve the effects of large extraction volume, simple process, and improved thermal efficiency
- Summary
- Abstract
- Description
- Claims
- Application Information
AI Technical Summary
Problems solved by technology
Method used
Image
Examples
Embodiment Construction
[0035] A boiler flue gas purification method mainly includes the following steps:
[0036] (1) Extract 30% of the air volume from the secondary air of the coal-fired boiler, and spray it into the upper part of the boiler at high speed. The location where the secondary air is injected is located below the refraction angle on the front wall or side wall of the boiler. The speed of injection is 150m / s, and two rows\14 nozzles are used to inject in an asymmetric injection mode.
[0037] (2) Simultaneously spray limestone mud, a by-product of steelmaking, as a sulfur adsorbent. The position where the limestone mud is injected is at the same height or above the position where the secondary air is injected, and the temperature of the limestone mud is 980-1100°C. Both the secondary air nozzle and the limestone slurry nozzle adopt adjustable nozzles.
[0038] Such as figure 1 As shown, at position 1, extracting 30% of the secondary air volume of the coal-fired boiler can reduce the...
PUM
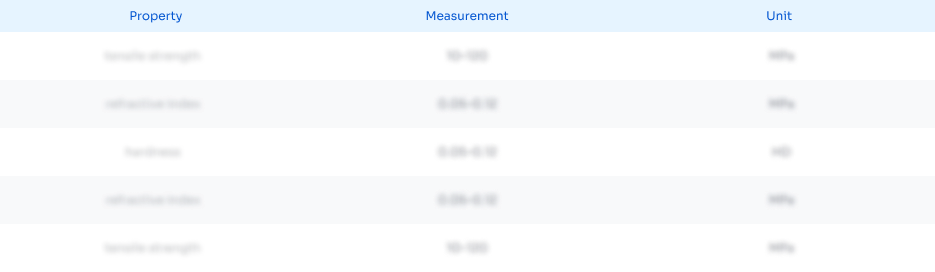
Abstract
Description
Claims
Application Information

- R&D
- Intellectual Property
- Life Sciences
- Materials
- Tech Scout
- Unparalleled Data Quality
- Higher Quality Content
- 60% Fewer Hallucinations
Browse by: Latest US Patents, China's latest patents, Technical Efficacy Thesaurus, Application Domain, Technology Topic, Popular Technical Reports.
© 2025 PatSnap. All rights reserved.Legal|Privacy policy|Modern Slavery Act Transparency Statement|Sitemap|About US| Contact US: help@patsnap.com