Highly corrosion resistant R-Fe-B magnet and preparation method thereof
A corrosion-resistant, magnet technology, applied in the direction of magnetic objects, inductors/transformers/magnet manufacturing, magnetic materials, etc., can solve the problems of great difficulty and risk, and not completely solve the problems of magnet anti-corrosion defects, so as to achieve the effect of improving anti-corrosion ability
- Summary
- Abstract
- Description
- Claims
- Application Information
AI Technical Summary
Problems solved by technology
Method used
Examples
Embodiment 1
[0025] The 45M magnet is made by ordinary powder metallurgy sintering method:
[0026] 1: Use the formula of Nd23%Pr7%Dy1%B1.0%CO0.5%Cu0.1%Al0.2%Fe67.2% (mass percentage) to melt in a vacuum melting furnace into a steel ingot with a thickness of less than 25mm;
[0027] 2: Use a secondary crusher to break into particles smaller than 20 mesh;
[0028] 3: Finely pulverize into 3-5um powder with jet mill;
[0029] 4: Pressed into a cylindrical magnet of D14*30;
[0030] 5: Sinter in a vacuum sintering furnace at 1080-1105°C for 1-3 hours, and age at 920° for 1-2 hours;
[0031] 6: Grind the outer circle and slice it into a D14*1.5 magnet;
[0032] 7: All magnets are chamfered, pre-treated by pickling, and the magnets aged at 530°C are directly plated with NI-CU-NI;
[0033] 8: The magnet is treated in 90wt% Zn-10wt% Al M alloy at a constant temperature of 530 ° for 3 hours, and then the magnet is taken out of the M alloy and placed in a cooling box with an inert gas and gas-q...
Embodiment 2
[0035]The magnet is treated in a metal alloy of 90wt% Zn-10wt% Al at a constant temperature of 530°C and a pressure of 100mpa for 1 hour, and then the magnet is taken out of the metal alloy and placed in a cooling box with an inert gas. Cool, and then do electroplating NI-CU-NI treatment.
[0036] All the other steps are the same as in Example 1.
PUM
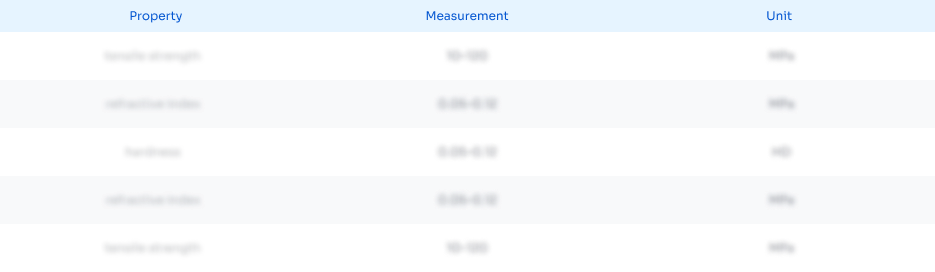
Abstract
Description
Claims
Application Information

- Generate Ideas
- Intellectual Property
- Life Sciences
- Materials
- Tech Scout
- Unparalleled Data Quality
- Higher Quality Content
- 60% Fewer Hallucinations
Browse by: Latest US Patents, China's latest patents, Technical Efficacy Thesaurus, Application Domain, Technology Topic, Popular Technical Reports.
© 2025 PatSnap. All rights reserved.Legal|Privacy policy|Modern Slavery Act Transparency Statement|Sitemap|About US| Contact US: help@patsnap.com