Method for preparing manganous carbonate by using waste slag and waste water containing manganese as raw materials
A technology of manganese waste residue and manganese carbonate, applied in chemical instruments and methods, manganese compounds, inorganic chemistry, etc., can solve the problems of polluting the environment, wasting mineral resources, etc., achieving high recovery rate, low cost, and reducing emissions and environmental pollution. Effect
- Summary
- Abstract
- Description
- Claims
- Application Information
AI Technical Summary
Problems solved by technology
Method used
Examples
Embodiment 1
[0025] Put the manganese-containing waste residue (about 50 grams) and waste water (about 1000 grams) of anisaldehyde prepared by manganese dioxide oxidation into the reactor, heat, slowly add 24 grams of oxalic acid under stirring, react at 80 ° C for 30 minutes, filter . Add 5 grams of 30% hydrogen peroxide solution to the filtrate, heat it, and add 115 grams of 25 percent ammonia solution at the same time, adjust the pH to 5.5, react at 40° C. for 30 minutes, and filter. The filtrate was heated to 60°C, and 5 g of ammonium sulfide solution with a mass fraction of 5% was added to adjust the pH ≈ 6.0, reacted at 60°C for 2 hours, and filtered. Add 34 grams of ammonium sulfate solids to the filtrate, heat and dissolve, then concentrate and crystallize to obtain 350 grams of ammonium manganese sulfate crystals. The recovery rate of divalent manganese is 79.5%.
Embodiment 2
[0027] Put manganese-containing waste residue (about 50 grams) and waste water (about 1000 grams) of anisaldehyde prepared by oxidation of manganese dioxide into the reactor, heat, slowly add 32 grams of oxalic acid under stirring, react at 75 ° C for 30 minutes, filter . Add 10 grams of 30% hydrogen peroxide solution to the filtrate, heat it, and add 125 grams of 25 percent ammonia solution at the same time, adjust the pH to 6.0, react at 50° C. for 30 minutes, and filter. The filtrate was heated to 60°C, and 4 grams of ammonium sulfide solution with a mass fraction of 5% was added to adjust the pH to 6.5, reacted at 65°C for 2 hours, and filtered. Add 60 grams of ammonium sulfate solids in the filtrate, heat and dissolve, then concentrate and crystallize to obtain 343 grams of ammonium manganese sulfate crystals. The recovery rate of divalent manganese is 77.9%.
Embodiment 3
[0029] Put the manganese-containing waste residue (about 50 grams) and waste water (about 1000 grams) of anisaldehyde prepared by manganese dioxide oxidation into the reactor, heat, slowly add 20 grams of oxalic acid under stirring, react at 90 ° C for 15 minutes, filter . Add 5 g of 30% hydrogen peroxide solution to the filtrate, heat it, and add 116 g of 25% ammonia solution at the same time, adjust the pH to 5.5, react at 40° C. for 30 minutes, and filter. The filtrate was heated to 60°C, and 5 g of ammonium sulfide solution with a mass fraction of 5% was added to adjust the pH ≈ 6.0, reacted at 60°C for 2 hours, and filtered. Add 34 grams of ammonium sulfate solids to the filtrate, heat and dissolve, then concentrate and crystallize to obtain 340 grams of ammonium manganese sulfate crystals. The recovery rate of divalent manganese is 77.2%.
PUM
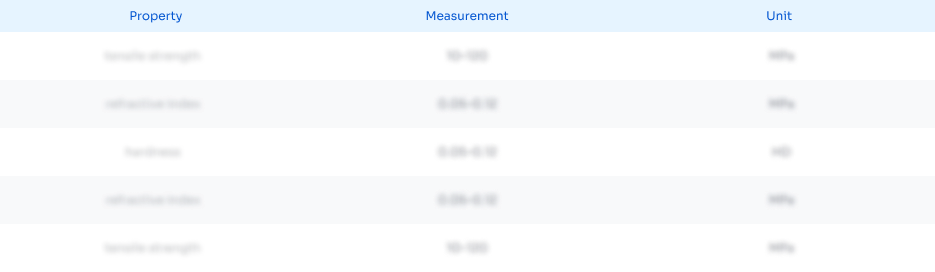
Abstract
Description
Claims
Application Information

- R&D
- Intellectual Property
- Life Sciences
- Materials
- Tech Scout
- Unparalleled Data Quality
- Higher Quality Content
- 60% Fewer Hallucinations
Browse by: Latest US Patents, China's latest patents, Technical Efficacy Thesaurus, Application Domain, Technology Topic, Popular Technical Reports.
© 2025 PatSnap. All rights reserved.Legal|Privacy policy|Modern Slavery Act Transparency Statement|Sitemap|About US| Contact US: help@patsnap.com