Fiber filling agent for rubber
A filler and fiber technology, which is applied in the field of rubber fiber filler, can solve the problems of rubber consumption, environmental impact, and complex process, and achieve the effects of simple process steps, reduced production costs, and omitted processing procedures
- Summary
- Abstract
- Description
- Claims
- Application Information
AI Technical Summary
Problems solved by technology
Method used
Examples
Embodiment 1
[0023] Grind the wheat straw with a ball mill first, then take 1000g of the crushed fiber, add 150g of water, 50g of glycerin, 50g of sorbitol, and 50g of polyvinyl alcohol, mix evenly with an internal mixer, dry and pulverize to prepare a particle size of Relatively small thermoplastic fiber ultrafine powder. Add 0.5% coupling agent, mix well and set aside.
[0024] Take 10g of the superfine fiber composite powder and mix it with 100g of natural rubber at 70°C, add 1.0g of vulcanizing agent and 1.0g of vulcanization accelerator at the same time; Under vulcanization for 15min.
Embodiment 2
[0026] First grind the rice husk with a ball mill, then take 1000g of the crushed fiber, add 150g of water, 50g of glycerin, 50g of sorbitol, and 50g of polyvinyl alcohol, mix evenly with an internal mixer, dry and grind to prepare a particle size of Relatively small thermoplastic fiber ultrafine powder. Add 0.5% coupling agent, mix well and set aside.
[0027] Take 10 g of the superfine fiber composite powder, and knead together with 100 g of natural rubber at 80° C., and add 1.0 g of vulcanizing agent and 1.0 g of vulcanization accelerator at the same time. The mixing process takes about 20 minutes, and the prepared rubber is vulcanized at 170° C. for 15 minutes.
PUM
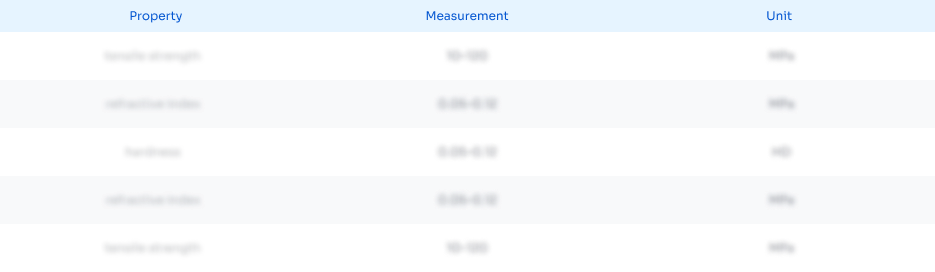
Abstract
Description
Claims
Application Information

- R&D Engineer
- R&D Manager
- IP Professional
- Industry Leading Data Capabilities
- Powerful AI technology
- Patent DNA Extraction
Browse by: Latest US Patents, China's latest patents, Technical Efficacy Thesaurus, Application Domain, Technology Topic, Popular Technical Reports.
© 2024 PatSnap. All rights reserved.Legal|Privacy policy|Modern Slavery Act Transparency Statement|Sitemap|About US| Contact US: help@patsnap.com