Method for preparing biomass oil in microwave thermal decomposition way
A biomass oil and biomass technology, which is used in the preparation of liquid hydrocarbon mixtures, petroleum industry, etc., can solve the problems of insufficient liquefaction reaction advantages, great difficulties, serious friction and wear on high temperature walls, and achieve accurate and controllable pyrolysis temperature. , Reduce the cost of pretreatment, the effect of reducing particle size requirements
- Summary
- Abstract
- Description
- Claims
- Application Information
AI Technical Summary
Problems solved by technology
Method used
Image
Examples
Embodiment 1
[0022] 50Kg granular waste wood chips are loaded into the raw material bin (about 3mm in particle size), and sent into the microwave pyrolysis reactor through a screw conveyor, and the feeding rate of the screw conveyor is set at 40Kg / h. The temperature of the sawdust entering the front end of the microwave pyrolysis reactor rises gradually to 90°C to 100°C after absorbing microwaves. Since the pressure inside the pyrolysis reactor is a slight negative pressure, reaching -0.02MPa, a large amount of water evaporates at this time. for the drying stage. Since the screw conveyor in the microwave pyrolysis reactor has a stirring function while conveying the sawdust, it promotes the uniform heating effect of the microwave. When the sawdust is transported to the middle section of the pyrolyzer, it starts to carbonize, and the temperature is in the range of 200°C to 350°C. At this time, it enters the carbonization stage. Since the carbonized sawdust absorbs microwaves dozens of times...
Embodiment 2
[0024] 30Kg section-shaped waste corn stalks are packed into the raw material bin (about 10mm in section length), and sent into the microwave pyrolysis reactor by a screw conveyor, and the feeding rate of the screw conveyor is set to 30Kg / h. The temperature of the straw entering the front end of the microwave pyrolysis reactor rises gradually to 90°C to 100°C after absorbing the microwave. Since the pressure inside the pyrolysis reactor is a slight negative pressure, reaching -0.02MPa, a large amount of water evaporates at this time, and the reaction The first stage is the drying stage. Because the screw conveyor in the microwave pyrolysis reactor has a stirring function while transporting the stalk, it promotes the uniform heating effect of the microwave. When the straw is transported to the middle section of the pyrolyzer, it starts to carbonize, and the temperature is in the range of 200°C to 250°C. At this time, it enters the carbonization stage. Since the microwave absor...
Embodiment 3
[0026]80Kg of the compressed straw sawdust mixture made by the granulator is packed into the raw material bin (5mm in particle diameter, 15mm in length), and sent into the microwave pyrolysis reactor by the screw conveyor, and the feed rate of the screw conveyor is set to 50Kg / h. The temperature of the material entering the front end of the microwave pyrolysis reactor rises gradually to 90°C to 100°C after absorbing microwaves. Since the pressure inside the pyrolysis reactor is a slight negative pressure, reaching -0.02MPa, a large amount of water evaporates at this time. for the drying stage. Because the screw conveyor in the microwave pyrolysis reactor has a stirring function while conveying the material, it promotes the uniform heating effect of the microwave. Carbonization begins when the material is transported to the middle section of the pyrolyzer, and the temperature is in the range of 280°C to 300°C, at this time it enters the carbonization stage. Since the microwa...
PUM
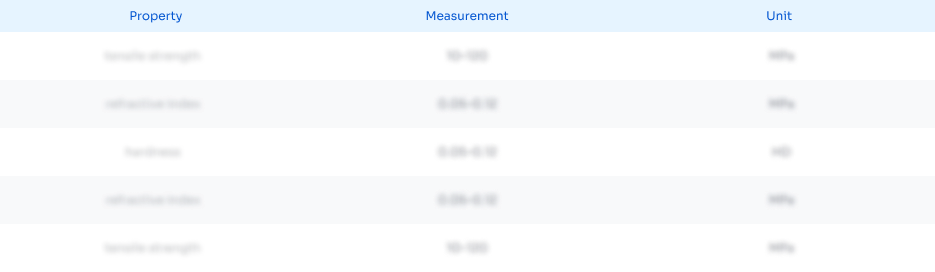
Abstract
Description
Claims
Application Information

- R&D
- Intellectual Property
- Life Sciences
- Materials
- Tech Scout
- Unparalleled Data Quality
- Higher Quality Content
- 60% Fewer Hallucinations
Browse by: Latest US Patents, China's latest patents, Technical Efficacy Thesaurus, Application Domain, Technology Topic, Popular Technical Reports.
© 2025 PatSnap. All rights reserved.Legal|Privacy policy|Modern Slavery Act Transparency Statement|Sitemap|About US| Contact US: help@patsnap.com