Process of using sulphur lead-zinc containing tailings to prepare sulphur iron ore concentrate
A technology of tailings and concentrates, applied in the direction of sulfur trioxide/sulfuric acid, chemical instruments and methods, wet separation, etc., to achieve the effects of reduced environmental impact, not easy to oxidize, and significant economic benefits
- Summary
- Abstract
- Description
- Claims
- Application Information
AI Technical Summary
Problems solved by technology
Method used
Image
Examples
Embodiment 1
[0019] Example 1. The tailings after flotation of lead and zinc in a lead-zinc ore dressing plant contain 7.50% sulfur and 10.82% iron. The sulfur-containing minerals are mainly pyrite and pyrrhotite, and the iron-containing minerals are mainly pyrite , pyrrhotite and a small amount of magnetite. Use a sieving machine to screen out the +0.15mm particle size, and the products under the sieve are pre-selected by a drum magnetic separator after pulping in a mixing tank, and the iron content is 50.30%, the sulfur content is 41.50%, the iron recovery rate is 42.16%, and the sulfur recovery rate is 35.68%. Magnetic separation of pyrite concentrate. The magnetic separation tailings contain 38% mud, and the spiral chute is used to remove the mud and throw the tails. The coarse concentrate is mixed with a mixing tank for flotation, and 2500g / t sulfuric acid is added to adjust the pH of the slurry to 5.5. 60g / t of terpineol oil was added as a foaming agent. After one roughing, two swee...
Embodiment 2
[0020] Example 2. The tailings after flotation of lead and zinc in a lead-zinc ore dressing plant contain an average of 12.80% sulfur and 11.18% iron. The sulfur-containing minerals are mainly pyrite, and the iron-containing minerals are also pyrite and pyrrhotite and the total amount of magnetite <1%. Due to the long storage time, the surface of pyrite minerals may be oxidized. Grind the tailings with a φ2100×2700 ball mill. The mud content of the product after grinding is 26%. Use a mixing tank to adjust the slurry and then carry out flotation. Add 3200g / t sulfuric acid to adjust the pH of the slurry to 5.5. Add butyl yellow 200g / t of pine oil, 80g / t of pine alcohol oil was added, and after two times of roughing, three times of sweeping and five times of beneficiation, 48.62% of sulfur, 42.47% of iron, 90.89% of sulfur and iron mixed grades were obtained, sulfur and iron The recovery rate of the pyrite concentrate is 88.87%, and the sulfur content of the final tailings afte...
PUM
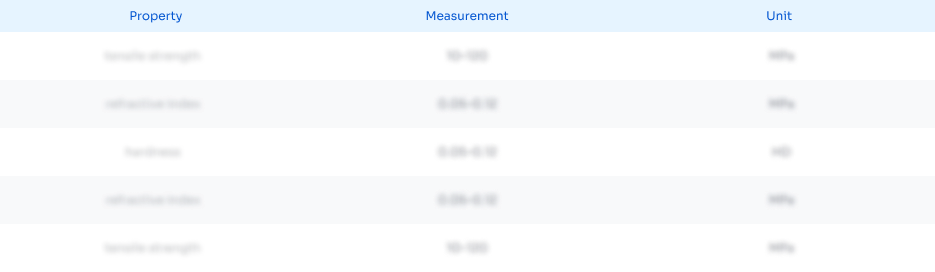
Abstract
Description
Claims
Application Information

- R&D Engineer
- R&D Manager
- IP Professional
- Industry Leading Data Capabilities
- Powerful AI technology
- Patent DNA Extraction
Browse by: Latest US Patents, China's latest patents, Technical Efficacy Thesaurus, Application Domain, Technology Topic, Popular Technical Reports.
© 2024 PatSnap. All rights reserved.Legal|Privacy policy|Modern Slavery Act Transparency Statement|Sitemap|About US| Contact US: help@patsnap.com