Raw material formula of tundish insulating board and preparation method for tundish insulating board
A technology of thermal insulation board and tundish, applied in the field of refractory materials, can solve the problems of high cost of thermal insulation board of tundish, high production cost, carbonization of molten steel, etc., and achieve the effect of reducing operators, long service life and simplifying production process
- Summary
- Abstract
- Description
- Claims
- Application Information
AI Technical Summary
Problems solved by technology
Method used
Examples
Embodiment 1
[0017] Embodiment 1, the raw material formula of the tundish heat insulation board, its raw material is composed of olive sand, magnesia, waste magnesia bricks, magnesium chloride, and hardener. The ratio of the raw materials (mass percentage) is 40% of olive sand, 21.5% of magnesia, 30% of waste magnesia bricks, 8% of magnesium chloride and 0.5% of hardener. The particle size of the raw materials is required to be no more than 3 mm for olive sand, such as 0.1 to 3 mm, no more than 3 mm for waste magnesia bricks, such as 0.1 to 3 mm, and 180 mesh for magnesia.
[0018] The preparation method of making the tundish heat insulation board by adopting the raw material formula of the above-mentioned tundish heat insulation board comprises the following steps:
[0019] 1) Configure raw materials and mix and stir;
[0020] 2) Add the stirred raw materials into water with 5.5% of the total mass of the raw materials, mix and stir for 3 minutes, and then put them into a mold for vibrati...
Embodiment 2
[0023] Embodiment 2, the raw material formula of the tundish heat insulation board, its raw material is composed of olive sand, magnesia, waste magnesia bricks, magnesium chloride, and hardener. The ratio of the raw materials (mass percentage) is 30% of olive sand, 25% of magnesia, 38.5% of waste magnesia bricks, 6% of magnesium chloride and 0.5% of hardener. The particle size of the raw materials is required to be no more than 3 mm for olive sand, such as 0.1-3 mm, no more than 3 mm for waste magnesia bricks, such as 0.1-3 mm, and 180 mesh for magnesia.
[0024] The preparation method of making the tundish heat insulation board by adopting the raw material formula of the above-mentioned tundish heat insulation board comprises the following steps:
[0025] 1) Configure raw materials and mix and stir;
[0026] 2) Add the stirred raw materials into water with 6.5% of the total mass of the raw materials, mix and stir for 5 minutes, and then put them into a mold for vibration mol...
Embodiment 3
[0029] Embodiment 3, raw material formula and preparation method of tundish heat insulation board, its raw material is composed of olive sand, magnesia, waste magnesia brick, magnesium chloride, hardener. The ratio of the raw materials (mass percentage) is 50% of olive sand, 15% of magnesia, 27.8% of waste magnesia bricks, 7% of magnesium chloride and 0.2% of hardener. The particle size of the raw materials is required to be no more than 3 mm for olive sand, such as 0.1-3 mm, no more than 3 mm for waste magnesia bricks, such as 0.1-3 mm, and 180 mesh for magnesia.
[0030] The preparation method of making the tundish heat insulation board by adopting the raw material formula of the above-mentioned tundish heat insulation board comprises the following steps:
[0031] 1) Configure raw materials and mix and stir;
[0032] 2) Add the stirred raw materials into water with a total mass of 7.5% of the raw materials, mix and stir for 4 minutes, and then put them into a mold for vibra...
PUM
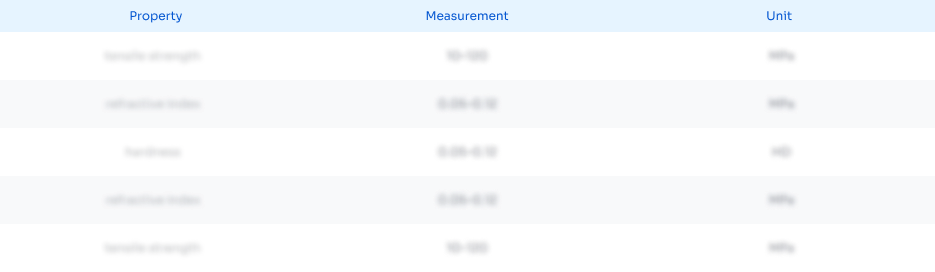
Abstract
Description
Claims
Application Information

- R&D
- Intellectual Property
- Life Sciences
- Materials
- Tech Scout
- Unparalleled Data Quality
- Higher Quality Content
- 60% Fewer Hallucinations
Browse by: Latest US Patents, China's latest patents, Technical Efficacy Thesaurus, Application Domain, Technology Topic, Popular Technical Reports.
© 2025 PatSnap. All rights reserved.Legal|Privacy policy|Modern Slavery Act Transparency Statement|Sitemap|About US| Contact US: help@patsnap.com