Major-minor cylinder combined rotor engine
A technology combining rotors and engines, applied in rotary piston engines, rotary or oscillating piston engines, combustion engines, etc., can solve the problems of increased fuel and oil consumption, long flame propagation path, large fuel consumption, etc., and achieve pollutant emissions. The effect of reducing the amount of waste, reducing pollutant emissions, and reducing fuel consumption
- Summary
- Abstract
- Description
- Claims
- Application Information
AI Technical Summary
Problems solved by technology
Method used
Image
Examples
Embodiment Construction
[0025] The present invention will be further described below in conjunction with accompanying drawing:
[0026] The embodiment of the present invention is that a master cylinder and three auxiliary cylinders are combined into a cylinder group engine. attached figure 1 to attach Figure 8As shown, the main and auxiliary cylinder combined rotor engine of the present invention is composed of main cylinder 1, auxiliary cylinder 2, 3, 4, rotor 5, 6, 7, 8, dividing plate 9, 10, 11, slide plate 12, 13, 14, 15 , Springs 16, 17, 18, 19, end caps 20, 21, shaft 22, bearing 23, spark plug 24 and the like. The inner cavities of the main cylinder 1 and the auxiliary cylinders 2, 3, and 4 are elliptical cylindrical, and the partitions 9, 10 are used between the main cylinder 1 and the auxiliary cylinder 2, the auxiliary cylinder 2 and the auxiliary cylinder 3, and the auxiliary cylinder 3 and the auxiliary cylinder 4. , 11 isolation, main cylinder 1, auxiliary cylinder 2, 3, 4 are coaxial...
PUM
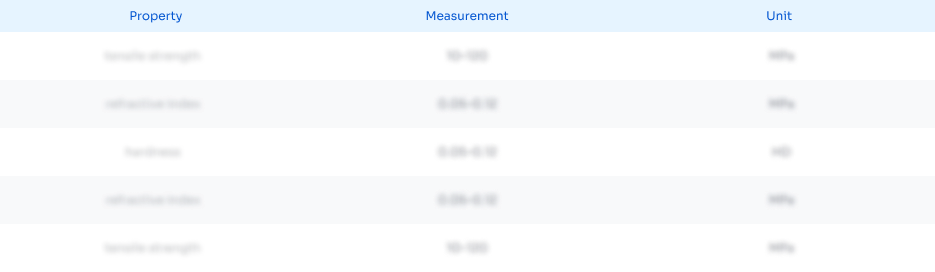
Abstract
Description
Claims
Application Information

- R&D Engineer
- R&D Manager
- IP Professional
- Industry Leading Data Capabilities
- Powerful AI technology
- Patent DNA Extraction
Browse by: Latest US Patents, China's latest patents, Technical Efficacy Thesaurus, Application Domain, Technology Topic, Popular Technical Reports.
© 2024 PatSnap. All rights reserved.Legal|Privacy policy|Modern Slavery Act Transparency Statement|Sitemap|About US| Contact US: help@patsnap.com