Method of preparing Octocrilene
A dehydrating agent and catalyst technology, which is applied in the field of octocrylene preparation, can solve problems such as environmental pollution, low yield, and octocrylene cannot meet the technical requirements for the manufacture of anti-ultraviolet additives, so as to improve work efficiency and energy utilization , simple processing, and convenient production and operation
- Summary
- Abstract
- Description
- Claims
- Application Information
AI Technical Summary
Problems solved by technology
Method used
Image
Examples
Embodiment 1
[0026] Add 364g (2.0mol) of benzophenone, 400g (2.0mol) of isooctyl cyanoacetate, 600ml of n-hexane, 247g (2.4mol) of acetic anhydride and 10g of ammonium acetate into a 2L four-necked flask, and install the water separator. Slowly raise the temperature to 85°C for reflux, separate the acetic acid-water-n-hexane solution, and reflux the n-hexane into the reaction system. GC online analysis of isooctyl cyanoacetate content is less than 0.5%, stop the reaction.
[0027] Cool down to room temperature, add cold water, stir for 30 minutes, statically separate the lower aqueous layer containing acetic acid-ammonium acetate, neutralize with ammonia water to pH 7, and concentrate to dryness to obtain ammonium acetate as a by-product. (The claim is heating and vacuum concentration, so how much degree of heating should be given, and what is the degree of vacuum? Give specific numbers, and the following examples are also modified accordingly) The oil layer is concentrated to recover n-he...
Embodiment 2
[0029] Add 509.6g (2.8mol) of benzophenone, 400g (2.0mol) of isooctyl cyanoacetate, 600ml of n-hexane, 247g (2.4mol) of acetic anhydride and 10g of ammonium acetate into a 2L four-necked flask, and install the water separator. Slowly raise the temperature to 85°C for reflux, separate the acetic acid-water-n-hexane solution, and reflux the n-hexane into the reaction system. GC online analysis of isooctyl cyanoacetate content is less than 0.5%, stop the reaction.
[0030] Cool down to room temperature, add cold water, stir for 30 minutes, statically separate the lower aqueous layer containing acetic acid-ammonium acetate, neutralize with ammonia water to pH 7-8, concentrate to dryness, and obtain ammonium acetate as a by-product. The oil layer was concentrated to recover n-hexane, and the concentrated solution was distilled under reduced pressure. Collection: 180-190°C / 0.1mmHg, to obtain 685.9g of light yellow viscous oily liquid with a yield of 95% and a purity of 99.5% (GC). ...
Embodiment 3
[0032] Add 364g (2.0mol) of benzophenone, 400g (2.0mol) of isooctyl cyanoacetate, 600ml of n-hexane, 494g (4.8mol) of acetic anhydride and 10g of ammonium acetate into a 2L four-necked flask, and install the water separator. Slowly raise the temperature to 85°C for reflux, separate the acetic acid-water-n-hexane solution, and reflux the n-hexane into the reaction system. GC online analysis of isooctyl cyanoacetate content is less than 0.5%, stop the reaction.
[0033] Cool down to room temperature, add cold water, stir for 30 minutes, statically separate the lower aqueous layer containing acetic acid-ammonium acetate, neutralize with ammonia water to pH 7, and concentrate to dryness to obtain ammonium acetate as a by-product. The oil layer was concentrated to recover cyclohexane, and the concentrated solution was distilled under reduced pressure, collected at 180-190°C / 0.1mmHg to obtain 655g of a light yellow viscous oily liquid with a yield of 90.7% and a purity of 99.5% (GC)...
PUM
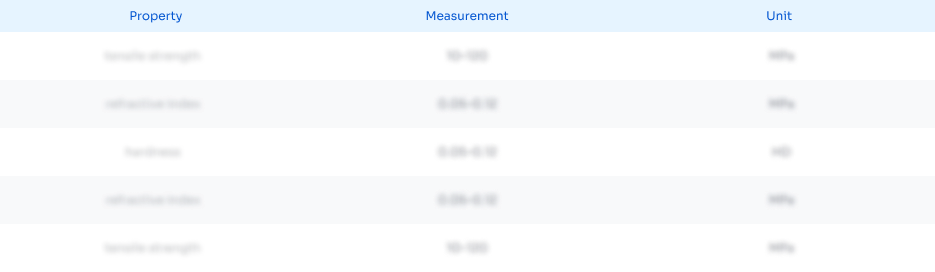
Abstract
Description
Claims
Application Information

- Generate Ideas
- Intellectual Property
- Life Sciences
- Materials
- Tech Scout
- Unparalleled Data Quality
- Higher Quality Content
- 60% Fewer Hallucinations
Browse by: Latest US Patents, China's latest patents, Technical Efficacy Thesaurus, Application Domain, Technology Topic, Popular Technical Reports.
© 2025 PatSnap. All rights reserved.Legal|Privacy policy|Modern Slavery Act Transparency Statement|Sitemap|About US| Contact US: help@patsnap.com