Fixed bed composite reaction equipment
A combined reaction and fixed bed technology, applied in chemical/physical processes, chemical instruments and methods, etc., can solve problems such as increase, excessive heat transfer, increase heat transfer temperature difference and enhance heat transfer
- Summary
- Abstract
- Description
- Claims
- Application Information
AI Technical Summary
Problems solved by technology
Method used
Image
Examples
Embodiment 1
[0023] The combined reaction equipment of the present invention is used for methanol synthesis reaction, uses water as cooling medium, adopts figure 2 The reaction equipment is shown. figure 2 A solid valve means the valve is closed, and a hollow valve means the valve is open. The steam drum 51 is connected to the heat exchange block area 21 and can be vaporized at a low pressure of 0.5-3 MPa, and the steam drum 52 is connected to the heat exchange block areas 22 and 23 and can be vaporized at a pressure of 1-5 MPa. The reaction gas reacts from top to bottom in the catalytic reaction block areas 31, 32, and 33. The upper part has a high reaction speed and a large reaction heat, and can react at a temperature of 230-280 ° C. There is a heat transfer temperature difference of tens of degrees between the inside and outside of the heat exchange block area 21 , The heat transfer block area 22, 23 outer catalyst layer reaction heat is small, can react at 220~270 ℃, the heat trans...
Embodiment 2
[0028] Embodiment 2: generate phthalic anhydride (B) with air catalytic oxidation o-xylene (A), literature shows (Zhu Bingchen editor-in-chief, chemical reaction engineering, Chemical Industry Press, P167), " raw material gas is air and o-xylene Toluene mixture, wherein o-xylene is 0.8432%, oxygen 20.33%, nitrogen 78.8268% (volume ratio), the main reaction heat of generating product is 1285KJ / mol, and the production side reaction CO, CO 2 The heat of reaction is 4561KJ / mol, with V 2 o 5 Titanium compound is used as catalyst, operating pressure is 0.1275MPa, shell-and-tube reactor tube inner diameter is 26mm, tube length is 3m, reaction tube is cooled by molten salt forced to circulate by pump, reaction gas feed gas concentration is 40.8g / m 3 , Airspeed 1500h -1 , when the molten salt temperature is 360°C, when the inlet gas temperature is 353°C and the bed depth is 0.8 meters, the hot spot temperature of the catalytic bed is 383.8°C, and when the bed depth is 2 meters, it is...
PUM
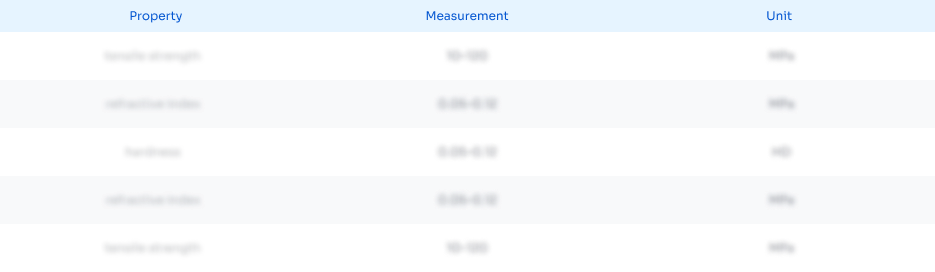
Abstract
Description
Claims
Application Information

- Generate Ideas
- Intellectual Property
- Life Sciences
- Materials
- Tech Scout
- Unparalleled Data Quality
- Higher Quality Content
- 60% Fewer Hallucinations
Browse by: Latest US Patents, China's latest patents, Technical Efficacy Thesaurus, Application Domain, Technology Topic, Popular Technical Reports.
© 2025 PatSnap. All rights reserved.Legal|Privacy policy|Modern Slavery Act Transparency Statement|Sitemap|About US| Contact US: help@patsnap.com